ASHP Ecodan L9 error - No Heating but Hot Water
My Mitsubishi Ecodan seems be be failing. I am getting a persistent L9 error which seems to indicate flow rate issues. My hot water still works fine and when this is running alone, no errors appear. The heating (rads upstairs, UFH downstairs via Heatmiser) does not work and the error appears when it comes on. I have checked the filter and a little debris appears but nothing major. The hot water pipes are all hot but none of the heating pipes are getting warm. I bled the rads upstairs but there was no air in them. Any idea what the issue could be before I call in a plumber? Has anyone suffered the same before?
I'm having exactly the same issue, so would also be interested if anyone has advice on this matter. I've followed the support videos from mistibishi but no luck. My problem got progressively worse over a few days. My 3 way valve changes over from water to heating perfectly fine, and there's piping hot water just after, so I know it's not that. When you feel the pipes the hot water doesn't seem to get passed the vertical pipe after the 3 way valve - not sure what's stopping it.
I reached out to Mitsubishi to provide potential insight into your issue.
L9 errors could arise from several factors, but ultimately, they indicate the system isn’t happy with the flow rate or can’t detect the flow. This situation typically requires a heating engineer to inspect the system.
The fact that your hot water mode works fine suggests that the heat pump, primary circulating pump, and flow sensor are functioning correctly. Assuming there isn’t an airlock, the issue likely lies with the zone valve or pump(s) on the heating side not operating as expected.
Recommendations:
- System Pressure: Check that the system is pressurised correctly.
- Air in the System: Ensure there’s no trapped air in the syste
- Settings: Verify that the DIP switches and the Main RC settings are configured properly.
- Valves and Pumps: Use a multimeter to confirm that the valves and pumps are being energised by the FTC controller.
- Multiple Circuits: If there are two heating circuits (e.g., radiators and underfloor heating), try isolating one. Start with the radiator circuit open and the underfloor circuit closed, and then reverse the configuration.
- Underfloor Heating Pump: Many underfloor heating manifolds include a dedicated pump, which could be causing the issue.
L9 indicates a flow rate issue when the system detects less than 5 l/min. The Mitsubishi ME Engineer App includes specific checks for this scenario.
The Homeowner Help-Line may request the make and model to provide tailored advice. They can also review fault logs via MelCloud to pinpoint the exact issues. Please call them.
If the hot water works properly, it’s likely the issue is on the secondary side (e.g., radiators or underfloor heating circuits). For example, if only one underfloor heating loop is calling for heat and the flow rate is below 2 l/min, the system will trigger an L9 fault.
To confirm flow rates, access the controller’s service menu, navigate to Running Information, and enter the code 540. The flow rate (in l/min) will display above the code.
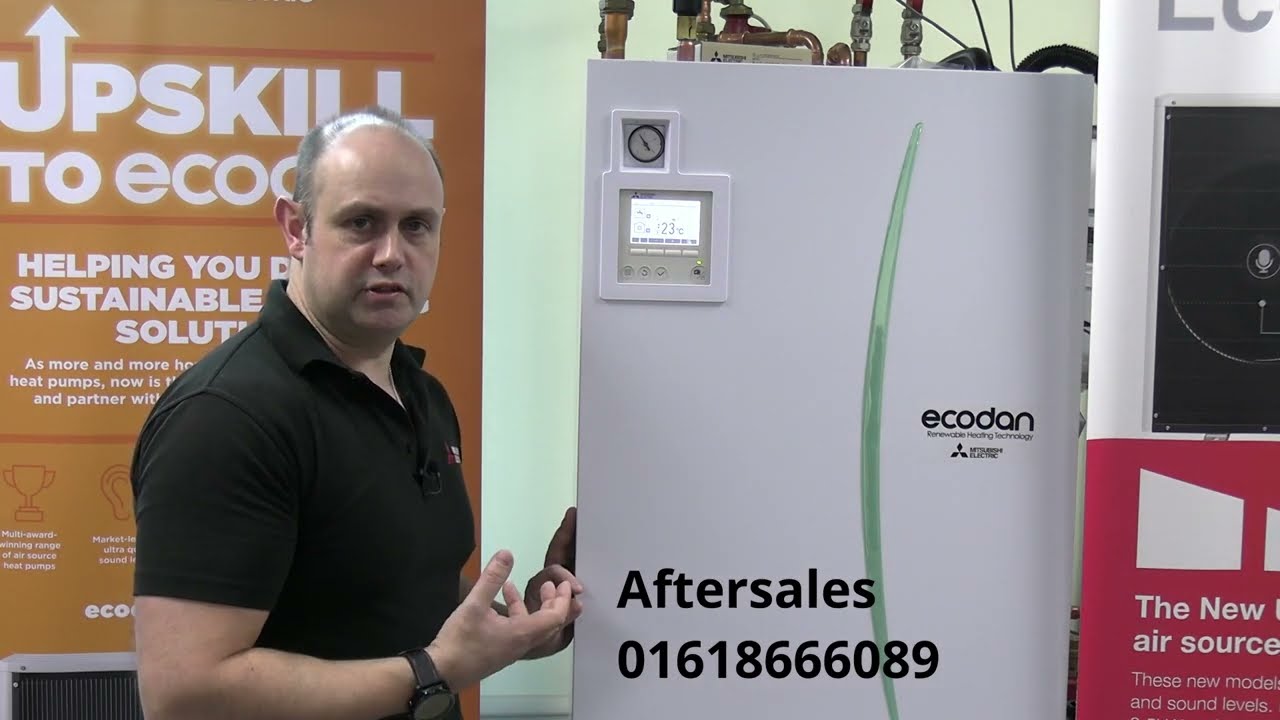
Pre-order: The Ultimate Guide to Heat Pumps
Subscribe and follow our Homeowners’ Q&A heat pump podcast
Thanks for this Mars. I've actually found out the issue, so this could potentially fix your problem Phonix.
It was the 'head' of the 3 port valve. It was seizing up inside the body - the heating side anyway.
A little wd40 and it seems to be working, but will have to order new one ASAP before it seizes again.
@dnagre delayed reply! It worked again for a bit but has started up with the L9 error again and I have noticed the valve is making a noise when trying to switch from heating to hot water- not a good noise. May sound like a silly question but how did you add wd40 to it? There's nothing I can see to remove or move to add anything like this. Thanks in advance!
@phoenix15 Hi Phoenix, this is an automaticity differential bypass valve and is often placed to allow surplus flow to short cycle the main system and prevent stalling of the primary pump when in a mode that needs less flow (not usually needed on ASHP with variable speed pumps and the ASHP controlling both heat and hot water (it might be needed on e 3rd party cylinder set up in some limited cases). Is your Ecodan connected to Mitsubishi Pre-plumbed cylinder?
To give you some less obvious tips (no in the online or official sites) and to identify the L9 issue if all of the conventional checks don't work as I am sure many will point out to you about Y strainer, closed valves and failing flow rate. The clue may be in the fact the system is intermittently filing and the time of year (Spring) if you have TRV's fitted to radiators or heads on your manifolds to the UFH there is a slight chance that at this time of year the rooms are satisfying and closing their local controls valves, this in turn will firstly reduce the flow rate and cause the ASHP to cycle more but also and eventually close enough or all of the flow to cause an L9, this bypass valve may also prevent this though and just allow the ASHP to run in a circle and short cycle.
To overcome this in the short term (if you feel this is what could be causing this issue) Open every TRV to full on the North side of the building, set all bedrooms to 20 or No2 as a set back for over heat only and only set any other rooms on the south side of the building to 23 or No3 as a set back for solar gain. You must also then set your system up to Weather Comp to your design flow rate and between say 15 to -3, Once you notice the rooms if at all start to overheat turn off your heating all together or lower the weather curve which ever you find more comfortable.
L9 could be caused by the following:
Anything that partly or fully restricts the primary circuits and reduces the flow below 5/Lpm
The L9 fault code on a Mitsubishi Ecodan air source heat pump typically indicates a low water flow or flow-related issue. This can be due to several factors, including:Reddit+6forum.ovoenergy.com+6forum.ovoenergy.com+6
-
Water leak: A leak in the system can reduce water flow.
-
Strainer blockage: Debris can clog the strainer, impeding flow.Reddit
-
Pump function: The circulation pump may be malfunctioning or not operating at the correct speed.
In some cases, the L9 fault code may also be associated with high-pressure protection activation, which can result from:JustAnswer+2T&K Airpower Enterprises+2YouTube+2
-
Overcharged system: Excess refrigerant can cause high pressure.T&K Airpower Enterprises
-
Blocked airflow: Obstructions in the airflow can lead to high pressure.T&K Airpower Enterprises
-
Faulty pressure sensor: A malfunctioning sensor may incorrectly detect high pressure. T&K Airpower Enterprises
Troubleshooting Steps:
-
Check for leaks: Inspect the system for any visible water leaks.forum.ovoenergy.com+2Reddit+2forum.ovoenergy.com+2
-
Clean the strainer: Ensure the strainer is free from debris.T&K Airpower Enterprises
-
Inspect the pump: Verify that the circulation pump is operating correctly and at the appropriate speed.Log in or sign up to view
-
Check refrigerant levels: Ensure the system is not overcharged.T&K Airpower Enterprises
-
Clear airflow obstructions: Remove any blockages that may be restricting airflow.
-
Test the pressure sensor: Confirm that the pressure sensor is functioning properly.
Professional installer. Book a one-to-one consultation for pre- and post-installation advice, troubleshooting and system optimisation.
@phoenix15 just wondering did you eventually find the other filter. Many of the Mitsubishi installs don’t always use the Y strainer. Instead thy have an isolation valve with a built in mesh filter. This valve is located on the outside wall on the primary return pipe going back to the Heat Pump.
Here is a picture of one and I have arrowed the access-nut which needs to be unscrewed to remove the mesh filter.
(*Important note : the valve needs to be closed first before removing the nut to prevent the water emptying out onto the floor. And of course it could also contain hot water or glycol)
@phoenix15 I'm no plumber so please don't take this as gospel, but what I did is
1- turn system off
2- press a button behind housing to remove housing (where my finger is pointing to, but around the back)
3- isolate the water going into the system- I had two valves
4 - use a spanner to losen, slowly, the nuts around the 3 port valve- also in the pic, water will flow out so get a big bucket.
5- when you have the valve in your hand , look for the needle looking thing. Push and pull delicately with pliers whilst spraying wd40 to the circular opening ingredients on the left and right side of the cylinder.
I also know I need to get a powerflush to get rid of the detritus I have built up in the system. This should hopefully boost flow rate too. Good luck
@sunandair don't seem to have this outside either
Only that!
I'm going to have to cave and get someone in to take a look. Can't get hot water tank past 31 degrees today without it throwing the L9!
Posted by: @phoenix15I'm going to have to cave and get someone in to take a look. Can't get hot water tank past 31 degrees today without it throwing the L9!
That’s interesting, but obviously concerning also…. Do you know how to access the flow rate enquiry menu on your main controller? IE the screen enquiry where you enter the 540 code.
It’s in the Service Menu. Select SERVICE (with the tick button), select password (with the tick button) usually 0000.
Scroll down to Running Information and select it (with the tick button), key in code 540 using the +and- buttons and arrow buttons to move the curser and press the tick button.
the readout should be your flow rate in litres per minute.
The next step is sometimes very revealing…. Press the tick button every 3 to 5 seconds for 5 consecutive times. and confirm if the flow rate changes at all.
Can you confirm what flow rate you are getting each time you press the tick button?
if there is an intermittent blockage problem this may vary quite dramatically. If it remains constantly at your target flow rate then that’s one less consideration to cross off the list. It’s not un-common for debris to build up and interfere with the optical sensor.
let me know if you want to try this?
@sunandair it just says 0 the whole time so definitely an issue. We've been trying to get someone out to the property but keep getting let down - small town and not many people that will service these AHSPs. I've had to contact Mitsubishi and see if they can come out instead, waiting to hear from them.
I think we likely have a few issues tbh. The emergency hot water doesn't appear to work and I am also assuming a possible leak as the pressure isn't increasing when trying to fill. There are some damp pipes around one on the pumps, very small leak if it is one, but it had made the insulation on that pipe very wet over time, I assume. I've removed it and it's dried out but the point the pipe connects to the pump is still looking wet.
Hopefully Mitsubishi will get out to us soon...
- 26 Forums
- 2,153 Topics
- 47.3 K Posts
- 54 Online
- 5,673 Members
Podcast Picks
Latest Posts
-
RE: Can you help with our research: solar panels, EV chargers, home batteries, heat pumps?
Nice one @toodles... always appreciate your enthusiasm ...
By Mars , 12 hours ago
-
@profzarkov Good to know in case it ever happens to me...
By bontwoody , 16 hours ago
-
RE: New Vaillant aroTherm Plus in black - When will it come to the UK?
@patrickvito We have had car dealers re-powder coat the...
By ASHP-BOBBA , 17 hours ago
-
RE: Are Octopuses Slowing Consumer Adoption of Heat Pumps?
I mean, is this surprising? The local installers in my ...
By Alex , 17 hours ago
-
@old_scientist sorry, I should have made it clear that ...
By GrahamF , 18 hours ago
-
RE: Mitsubishi Ecodan 11kw Defrosting Issue.
@thundermink can you provide photos to illustrate your ...
By Morgan , 18 hours ago
-
RE: Boiling Mad: Exposing Radiatorgate
Hi @Rob, I’d be more than happy to contribute. I have ...
By DREI , 20 hours ago
-
RE: Solar Power Output – Let’s Compare Generation Figures
@andris a great year - very happy with our system
By Profzarkov , 22 hours ago
-
RE: A Customer's Lessons Learnt from a Heat Pump Installation in a Large House
After our rather lengthy meander off piste, I thought I...
By GrahamF , 24 hours ago
-
RE: Midea ASHP – how to set weather compensation
@pash44pump - to collect the IAT/OAT data, can I sugges...
By cathodeRay , 1 day ago
-
RE: Ecodan software update. Real or scam?
@vinz86 Contact Mitsubishi and an engineer attends and ...
By ASHP-BOBBA , 1 day ago
-
@drei When I was in local government we were of cours...
By JamesPa , 2 days ago
-
RE: Heat Pump SCOPs – The Truth Might Not Be What You Think
Sufficient system volume is also essential for ensuring...
By Old_Scientist , 2 days ago
-
RE: Flexi-Orb Heat Pump Scheme: A Game-Changer for the UK's Heat Pump Industry
As someone who has suffered from a Heat Pump installati...
By DREI , 2 days ago
-
RE: What crazy nonsense are inverter limits and why are they imposed?
I’ve also got a dual fuel Rangemaster. We originally ha...
By Majordennisbloodnok , 3 days ago
-
RE: Octopus tariffs - a quick comparison
@tim441 I’d agree wholeheartedly with that, with 2 x Po...
By Toodles , 3 days ago
-
RE: Electricity price predictions
@bontwoody Maybe one for @editor to consider whether a ...
By ChandyKris , 3 days ago
-
RE: is a home battery without an EV worth it?
You would think, but when I had my Powerwall 3 installe...
By Old_Scientist , 3 days ago