Heat pumps are becoming increasingly popular as they provide an efficient and eco-friendly way to heat homes, helping us save money and protect the environment. However, to work best, they need the right setup. Sometimes, parts like low-loss headers and buffers, which are supposed to help, can actually reduce the heat pump’s effectiveness. This can lead to less warmth and higher running costs. It’s important to understand why these parts might not always be beneficial and what you can do to get the most out of your heat pump.
The Two Pillars of Heat Pump Prowess
Understanding how heat pumps operate holds the key to optimising their performance. Two fundamental principles guide their efficiency:
1. Low-Temperature Symphony: Think of heat pumps as musicians, capable of raising the temperature of heat, much like conductors orchestrate notes. But here’s the twist: the lower the target temperature, the less energy they need to play their magic. So, aiming for a cosy 20C instead of a sweltering 25C translates to a lighter burden on the system and a lighter burden on your wallet.
2. Flowing River of Warmth: Heat pumps move heat through water flowing through your radiators and/or underfloor heating. Imagine this water as a river, where a smooth, steady current efficiently delivers the thermal energy. Now, picture what happens if you dam the river with restrictions like narrow pipes or sluggish pumps. The flow suffers, and the heat struggles to reach its destination, leaving you feeling chilly despite the pump working overtime.
The Deceitful Decoys
Low-loss headers and buffers are often recommended by many installers and manufacturers as beneficial additions to heat pump systems. They are touted to enhance efficiency and comfort. However, in practice, the benefits they promise may not always materialise as expected. Let’s see why:
Low-Loss Header Trap: These headers aim to minimise heat loss in the pipework, but they often achieve this by reducing the water flow. Remember our river analogy? A constricted header acts like a dam, hindering the smooth flow and consequently, the efficient transfer of heat. This leads to the dreaded high delta T situation – a large difference between the temperature of the water entering and leaving your radiators. It’s like the conductor demanding the orchestra play at full volume while restricting the air to their instruments. The result? Strained performance and disappointing results.
The Buffer’s Misdirection: Buffers are essentially storage tanks for hot water, supposedly providing you with readily available warmth and reducing the heat pump’s workload. But here’s the catch: buffers add complexity and introduce additional heat loss points. They essentially become thermal cul-de-sacs, where some of the precious heat gets trapped and wasted. Additionally, buffers can encourage inefficient on-off cycling of the heat pump, further negating any potential gains.
Beyond the Decoys: A Path to Optimal Performance
So, how do you ensure your heat pump system lives up to its full potential? The key lies in simplicity and a focus on the two core principles we discussed earlier:
1. Embrace the Flow: Ditch the low-loss headers and any other flow-restricting components. Let the water flow freely, like a well-maintained river, ensuring efficient heat transfer throughout your home.
2. Befriend the Low-Temperature Symphony: Ensure your temperature control is managed directly by the heat pump’s controller, as on-off thermostats can be less efficient than a buffer. It’s crucial for the thermostat to be integrated with the system for optimal efficiency, rather than relying on standalone on-off mechanisms.
3. Weather Compensation – Your Wise Companion: Utilise weather compensation, a feature that automatically adjusts the heat pump’s output based on the outdoor temperature. This ensures constant comfort while minimising energy consumption. Think of it as a dynamic conductor, adapting the orchestra’s performance to the changing weather conditions.
4. Delta T – The Fine-Tuning Maestro: Implement delta T control, which fine-tunes the temperature difference between the flow and return water. This further optimises the heat pump’s operation, squeezing out every drop of efficiency. Consider it the musical equivalent of perfect intonation, ensuring a harmonious performance from your heating system.
5. Radiator Harmony: Use thermostatic radiator valves (TRVs) only in bedrooms, allowing weather compensation and the heat pump itself to manage the temperature in common areas. This strikes the perfect balance between individual comfort and overall system efficiency.
6. Hot Water Wisdom: Optimise your hot water production too. Let the heat pump controller handle this task. Think of it as a bonus track in the symphony of energy savings.
Avoiding the Heat Pump Villain
Sometimes, navigating the world of heat pump installation can feel like a quest through a confusing landscape. If you’re still daunted, consider buying my book Bodge Buster.
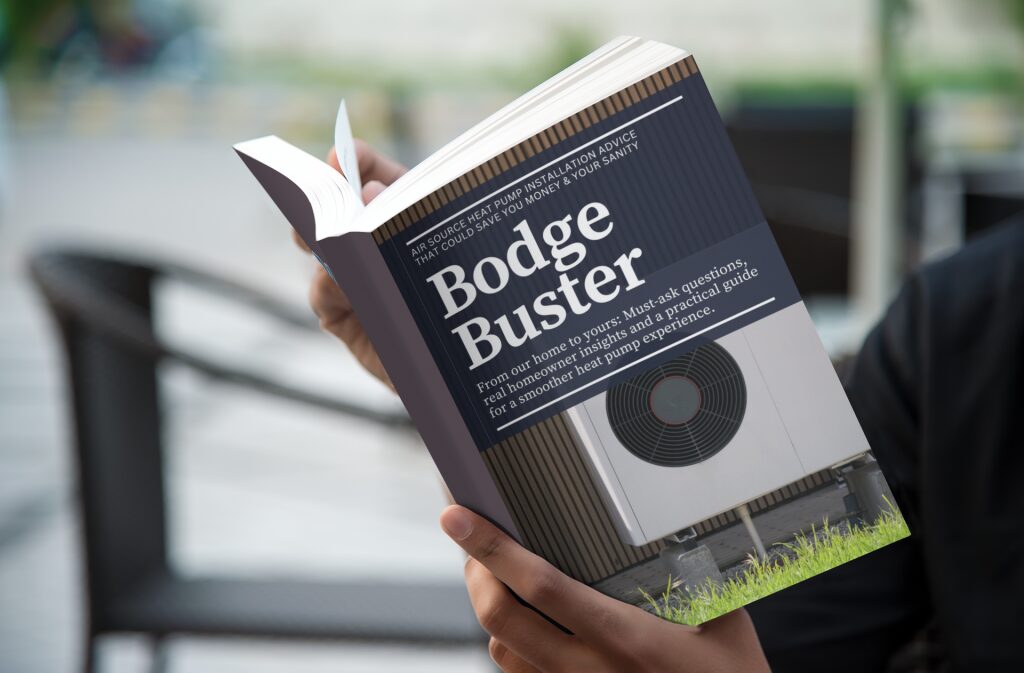
Manufacturers and even some training bodies might recommend setups that prioritise their own interests over your comfort and efficiency. Remember, you’re the homeowner, the conductor of your heating symphony – a poorly installed system not only strains your wallet but also leaves you in the discomfort of a cold home, bearing the full impact of such shortcomings. Don’t hesitate to question proposed designs, seek information from independent sources, and prioritise simplicity and the two core principles of low-temperature operation and optimal flow.
By taking charge and avoiding the deceptive decoys, you can ensure your heat pump delivers the comfort and sustainability you deserve, turning your home into a haven of warmth and energy efficiency. So, banish the monsters and villains, embrace the flow and let your heat pump play its beautiful low-temperature symphony.
Well said!
I (and I suspect many others) have met a fair few installers who don’t seem to accept this!
Thank you Mars, I accept that a LLH may affect the efficiency of the overall efficiency – but how can the average individual who has a system installed with a LLH know whether they would be better off without it? Ripping apart a system that has one such and a secondary pump is a little radical – and is ther any guarantee that the efficiency would improve without these components. Presumably, LLH was a concept with a purpose – is it just to protect the designer and installers? Regards, Toodles.
@Toodles It is purely there to allow the heat pump to operate without any flow errors… Primary side just sits there running into the header, microbore or TRVs closing don’t have any effect on it.
@HughF If a system doesn’t have any variable restrictions like TRV’s, would such a system be better able to perform to the optimum without an LLH then? My system has carefully adjusted lockshield valves (constant restrictions in other words) but does have one TRV in a bedroom. There is an LLH and secondary pump – I was told this means achieving a Delta T of 5 degrees across the radiators is not crucial as the LLH is acting as an intermediary. Regards, Toodles.
Hi @Toodles don’t know if you’ve seen them before but there a couple of articles which may be of interest from Protons for Breakfast regarding his system performance before and after removal of the LLH (I have a LLH on my Daikin ASHP) – links here and here
@Marzipan71 Thanks very much Marzipan, very interesting indeed. I think that that data excuses my uncertainty of LLH – Good or Bad? Regards, Toodles.
Having looked at the two articles, I think that the author seems to be arriving at conclusions on very limited data.
I also note with interest that he appears to have failed to appreciate the reason why the IAT increased to 22C after the LLH was removed, the transfer of thermal energy was much improved, so the LWT was now higher than required. Had he lowered the WC curve to lower the IAT, I think that he would achieved an increase in efficiency and higher COP.
It’s a fair question
There are two approaches to answering it I can think of.
1. Measure the flow-flow temperature drop across the llh. For each degree you are losing 2-3% system efficiency.
2. Plumb in bypasses for the llh on the flow side and for the secondary pump with a couple of manual diverter valves so you can switch them in and out. Perform the experiment
In most cases it seems, yes.
One might reasonably ask, why is the heat pump designed to register them as errors. Answer – because the situation shouldn’t occur.
Putting sticking plaster over a red warning light doesn’t make the problem go away. However it does reduce the liklihood of call outs. Now who does that help?
On commissioning, I was having a nightmare getting rid of flow errors, I suspected a faulty flow switch so just jumpered it out in the terminal strip. It has been running like that since september.
Turned out to be air in the system. Haven’t had a flow error since 😀
Your perspective on the matter is both practical and grounded. The decision to alter a heating system with a LLH and secondary pump hinges on a balance between current system performance and the potential for improved efficiency.
At a personal level, if your system is achieving a SCOP of 3 or more, maintaining a warm house without noticeable inefficiencies or discomfort, then the system can be considered effective. In such a case, the idea of overhauling the system might indeed seem unnecessary.
My own experience echoes a similar sentiment but also highlights the complexities involved. Our system, equipped with four distribution pumps, was designed to efficiently distribute heat throughout. However, in reality, it achieves a SCOP of 2.71, which indicates that it’s not operating at optimal efficiency. This lower SCOP points towards potential inefficiencies, possibly exacerbated by the current configuration with the buffer and multiple pumps.
It’s essential to recognise that LLHs are designed with specific purposes in mind – in theory, they help maintain consistent flow rates, prevent short-cycling of the heat pump and can contribute to system longevity. However, their impact on efficiency isn’t universally beneficial and can vary based on the system’s design and the property’s heating requirements.
@Toodles
graham hendra wrote an article on why llhs used to be needed and aren’t needed any more
Or at least that’s how I understood the article he’ obviously one of the experts! Been there, done that!
@Judith Very interesting, it rather sounds as though the installers need to update their knowledge of modern products then they might take advantage of the latest designs and we could all benefit in the long run. Regards, (and thanks) Toodles.
It’s both very refreshing and somewhat depressing to read this. Assuming I understand it correctly there is an admission that LLHs were added principally to stop tech support calls, with the justification that installers got the set up that would, even then, have worked without a LLH wrong. I don’t think we have reason to doubt the rationale, although some installers may consider it a bit of a slur.
Then there follows a clear statement that things have changed in the product world, and they are no longer necessary.
There is an element of coming clean (excellent) but also an element of we were doing a bad thing, we knew it, but it was someone else’s fault (not so good).
What is unequivocally good is that its out in the open.
Are all Low Loss Headers bad? Mine was fitted as per Samsung schematics. This I would imagine would remain part of the warranty agreement. The effect on my system seems to be negligible. I did discusses this at a resent service and the engineer comment was “if its not broken don’t fix it". As my efficiency appears to be high, 2288kw/h energy use over a year as opposed to 1700litres (17000kw/h) of oil it seems my system is working OK. Another point is if by removing the LLH increases efficiency could it have an effect on the size of HP fitted? One other point, can a LLH act as a debris trap for older heating system thereby protecting the HP?
@prjohn Ooooh! Mars! Did you consider you might be opening a massive can of worms with this topic?! ;-)))
Always good to have discussions about topics like this.
And as i point out above, its easy to work out roughly how much its costing. Measure the flow to flow temperature drop across the llh and reckon on 2-3% loss in system efficiency per degree (if you want to be more precise, refer to the cop vs ft curves in the databook for youe machine). Add a few 10s of W for the second pump.
If you are happy with this leave the llh in place. If you are not then remove or bypass it.
@Mars Here is a graph of temperatures taken from my 4 pipe buffer tank ( before it was removed). You can see that Delta T between Buffer in (LWT) and Buffer return (RWT) is similar to the Delta T between Buffer out (to the radiators) and Radiator return (back to the buffer from the radiators). I take that to suggest that the flow rates in the primary and secondary circuits are similar. Nevertheless, there is a 4-5 degC difference between LWT from the Samsung and the temperature of the water going to the radiators. That in itself reduces efficiency and increases costs by around 12%.
Protons for breakfast found that removal of his LLH didn’t make much difference, but I wonder if his LLH was tall and thin as opposed to my buffer tank which was short and stout. There is only a couple of inches between the pipes in my buffer tank, so mixing is inevitable.
A simple remedy would be to re-pipe your buffer to make it into a volumiser in the return leg to the heat pump.
I’ve probably spent far too much time mulling over this topic. We’ve always had performance issues with the heat pump when temperatures drop. And it’s got nothing to do with the heat pump. If it’s set to deliver 45C water to the heating circuit, it does so without a problem. But this doesn’t translate into a warm, cosy room because the radiators are not receiving the heat they ought to.
To address this issue, our installers have returned multiple times, fitting K3 radiators and installing more distribution pumps. Now we have four distribution pumps, yet the distribution of heat remains sporadic, which is nuts.
Then I came across @Brendon Uys who was harping on about buffer tanks and how awful they are. “Yada, yada, yada," I thought at the time. There’s no way that buffers and LLHs can affect heating performance and I gave @Brendon Uys a hard time. So I went away and started to do more reading, and it’s fascinating just much these additions do affect heat pump systems.
Buffer tanks did play a crucial role in the evolution of the heating industry. Their introduction was a response to the inherent drawbacks of traditional on-off fossil fuel boilers. These older boilers needed to run at elevated temperatures, often exceeding 80C, to avert heat exchanger corrosion. For the period’s technology, operating at such high temperatures was deemed efficient, and utilising a buffer tank for temperature blending was beneficial. These earlier systems were also designed for lower flow rates, a stark contrast to the higher flow demands from multiple connected circuits. The introduction of buffer tanks helped manage these different needs more efficiently; but this belongs to an era that has since evolved, reflecting a different technological landscape than what we see today with heat pumps.
Because it’s so entrenched in the industry, there’s a common but incorrect belief that buffer tanks significantly assist heat pumps in balancing the load. The actual impact of a buffer tank on load management is quite limited. A buffer tank with a capacity of 100 litres (which is what we have at home) can only store around 1.17kW of energy when heated to a temperature 10C above the needed level. In a system requiring 10kW, this merely equates to a buffer duration of approximately 7 minutes, which is hardly noteworthy. Additionally, the extra effort to raise the temperature by that additional 10C could lead to an increase of as much as 25% in energy costs. And we have multiple distribution pumps trying to pump this water around the system, all of which have running costs too, for not that much effort.
This leads us to a critical point regarding the testing practices of heat pump manufacturers in the UK. While the performance and efficiency numbers they publish are derived from standardised testing conditions for consistency and reliability in comparing various models, the specifics of whether these tests include LLHs and buffer tanks are often not detailed in the general product literature.
According to information I’ve received from sources well-informed about the industry, most of these test setups do not incorporate LLHs or buffer tanks. Despite this, manufacturers frequently recommend their inclusion in actual installations. This discrepancy suggests that the performance results achieved in real-world settings may not align precisely with the published data, as the test conditions under which these figures are obtained do not fully mirror the recommended installation setups.
@Mars – interesting. If I may also borrow a quote and refer it to @Derek M:
I think this may be one of the problems encountered when modelling heat pump behaviour based on manufacturer data. The manufacturers quote efficacy (what can be achieved in ideal circs eg in a lab/RCT), whereas in the real world we get effectiveness (what can be achieved in practice, in the real world, where ‘stuff happens’). In medicine, the two are often very different, and I think the same might apply to heat pumps: what the labs predict is not what you get. And that’s before incorporating the PHE throttling effect (which is after all just another what you get in practice effect).
@cathodeRay, in addition to what you’ve mentioned above, the discrepancy between the performance and efficiency data cited by heat pump manufacturers (and by extension, the MCS) and the actual achievable outcomes in real-world installations is thought-provoking. This situation seems akin to the notable issue observed in the automotive industry, specifically the car emissions scandal, where the performance reported under test conditions did not accurately reflect real-world operation.
The heart of the issue lies in the testing environments and methodologies used by heat pump manufacturers. These tests are often conducted under idealised or controlled conditions that may not fully represent the typical installation scenarios or everyday usage patterns. Consequently, the efficiency and performance figures obtained in these test environments can be significantly higher than what a user might realistically experience.
Given the importance of time and resource efficiency in today’s world, it would indeed be revealing and beneficial if manufacturers could provide more transparency about their testing environments. Understanding the specifics of these test setups, including the conditions and parameters used, could offer valuable insights into how these figures are derived and their applicability to real-world settings.
This level of disclosure would not only aid consumers in making more informed decisions but could also push the industry towards more realistic and practical performance benchmarks. Our heat pump’s performance does not remotely match the numbers the heat pump is capable of according to the manufacturer. It would encourage a move away from idealised figures and towards data that better reflects the varied and sometimes challenging conditions of actual installations.
A call for greater transparency and realism in the performance data provided by heat pump manufacturers is not just about ensuring consumer trust; it’s also about aligning industry practices with real-world applications and expectations. Just as the automotive industry had to confront and adapt to the revelations of the emissions scandal, the heat pump industry could benefit from a similar shift towards greater honesty and clarity in its performance reporting.
@Mars Indeed, manufacturers of most devices have their own methods of measurement that do not always relate well to ‘real world’ situations; they provide a rough guide that should be taken with generous pinches of salt I think. OK, the last three days may not be typical of UK winter weather as it has been rather milder than of late. I attach a graph where I have just left in the (what I believe) salient pieces of data for the Daikin heat pump performance. The COP has just exceeded 4 whereas Daikin might have one believe that it might perform with a rather higher figure. There’s is an aspiration – mine was the achieved performance (with a LLH that they probably weren’t employing)! Regards, Toodles.
In fairness to the manufacturers I think that most of the critical tests are done to BS/EU standards, and they generally quote the numbers. The standards themselves will specify the test method/environment. I cant see why they would include a buffer tank/llh unless its a mandatory part of the installation according to the manufacturer.
How many heat pump manufacturers actually insist on system separation in their installation manual. From my recollection of when I read most of the manuals (about a year ago so my recollection is now imperfect). Some show one in a diagram which also includes a backup boiler (so basically an all-options diagram), in this case its clear that some form of separation is required, but is it fair to infer that the same applies when there is no backup boiler. I think its been more the installation industry that has pushed this approach because it eliminates a potential source of call out.
That is precisely why when modelling heating systems, not just the heat pump data should be part of the overall equation. It is also necessary to incorporate the effect from additional equipment and the limitations of the overall system design.
You are indeed correct, because in the real World installers include buffer tanks, LLH’s or PHE’s that are not normally required.
The other point to remember is that they are testing the heat pump, not a heating system.
There are low loss headers, damned buffers, and then there are plate heat exchangers. The usual Freedom wording for Freedom based Midea (and Samsung?) systems/installations appears to consider these one and the same, the point being hydraulic separation, not how it is achieved (though how a two pipe buffer achieves this is beyond me unless they have to be four pipe buffers). This is from the Freedom Midea installation manual:
“Every system must have hydraulic separation between the primary (heat pump) and secondary (heating circuit) pipe work.
This can be via a buffer tank, low loss header or plate heat exchanger. If you install the unit without hydraulic separation, you will void the warranty."
I’m pretty sure GH wrote that. It is useful, insofar as it hints at why they are essential (at least as far as keeping your warranty): the system “must have hydraulic separation between the primary (heat pump) and secondary (heating circuit) pipe work". That just leaves the question: why must it have hydraulic separation?
Moving on, and this is I think what @Toodles is getting at (as well as pointing out that changing the system by ripping bits out is disruptive), there is also a valid question as to whether in some way the the devices might also have benefits to the end user. Less glycol in my PHE setup is one possibility, no ex radiator crud flowing through the heat pump is another. There may be others.
That said, I am clear in my mind that my current PHE setup almost certainly throttles my system significantly when heat demand is high, though I do note @marzipan71’s links to posts showing the removal of a LLH (not a PHE) appears to have made no difference.
I just want to be sure that removing my PHE won’t (a) make no difference (as in @marzipan71’s links, though in that case it was a LLH) and (b) cause unwanted effects.
Incidentally, no reply yet from Freedom to my email asking about the details of my PHE.
And it is like compound interest, not just additive.
See my earlier quote (1:15pm) from the Freedom Midea Installation Manual (from 2022). The word used is ‘must’ (have hydraulic separation). I rather suspect if there is an equivalent Freedom Installation Manual for Samsung heat pumps, it may well say the same thing, or something very similar.
Thats from Freedom, what does the OEM actually say
Here is the system diagram from page 4 of the Midea manual. No buffer tank, LLH or PHE in sight.
I think the difference between testbed and realworld here vs others is that in say cars, you could never get the MPG advertised (although now there are more realistic test standards that give usable (ish) numbers).
But in this case the HP testbeds are all openloop (its not a secret) and you CAN get those numbers if you build a real world system that way. if you build with a buffer or llh or phe you will get a few % off parity at best, if it is engineered well (or you get lucky). If not, then a lot of % off. clearly we have both ends of that spectrum here, some are happy (ish), some are unhappy.
I also studied lots of vendor schematics and documents, and publications and youtubes from people who know what they are talking about . none of them say “you must have a buffer/llh/phe". the only reason the situation that has come about with them still being put in by default, is, as far as I can tell, is as a legacy of the earlier installer “rules of thumb" where they were all paranoid about getting flow rate issues causing the HP to error, so they’d mitigate that with one of these devices, and somehow its stuck. Only certain installers (plus most/all of the DIY’ers) are confident enough to go against this.
Take a look at the heatpumpmonitor.org system list, set “hydraulic separation" to on in the display, and sort by COP. The distribution isn’t perfect, and there are plenty of other reasons why one system can perform better than another as we know, but there is still a significant bias towards those with LLH/Buffer being lower down the list and those with None being higher. QED.
the other issues mentioned as reasons to keep these devices , aren’t. dirt – use a suitable low resistance filter. freezing – antifreeze valves.
the only reasons IMO to keep / put in those devices in a domestic setup are if
its already in, your system is performing reasonably well and the cost/hassle of removing it for a slightly better performance isn’t worth it
you have more complex system than usual which genuinely requires hydraulic separation . e.g. multiple heat sources. A real “buffer tank" (i.e. a big one , capable of storing a lot of heat) has a use case here as well, if one heat source is uncontrolled.
Spot on IMHO and my studying, like yours, of manuals, posts and the various other info available.
This is a variation on efficacy vs effectiveness. That’s what Midea say in their ‘ideal’ manual. In the real world, stuff happens, Freedom offer training courses and provide installation manuals, and that is what the installers use. Why wouldn’t they? Freedom are a major supplier, surely they know what they are talking about?
You will have to ask Freedom why they varied the spec from the Midea manual.
I suspect the problem relates to the fact that as far as I am aware TRV’s still have to be installed on heating systems, which was the norm with gas and oil boilers.
Heat pumps work much better without TRV’s or on – off type controls, but many are still included, because that is how it was always done for the past umpteen years.
So to prevent their ‘trained’ installers getting loads of call-outs because of low flow when the TRV’s started shutting down, Freedom decided it was necessary to insist on hydraulic separation, rather than produce correctly designed systems and train the installers correctly.
Maybe if they start loosing business due to all the free publicity they are getting then they may start doing their job correctly.
But it is just unrealistic to expect most people in the real world to do this. And there is a related question, should they be expected to do it?
no of course end users shouldn’t be doing this. Installers should. Installers should be MADE to put in systems that perform properly and held liable (not paid) if they don’t (perform properly).
In your case, freedom put their own rules around the system, in to protect themselves from “low flow" callbacks. plus someone underspecced the PHE. So you’ve ended up with a system design that would have worked within a few % if it was well engineered, but its NOT well engineered (the aforementioned PHE). Bizarrely you might have actually done better with an LLH! This is all unfortunate obviously for you and you have my sympathy, but doesn’t change my view on the bigger picture.
Interesting, I’ve just done what you suggest, but I don’t think it gets near a QED threshold, and as we all know, and you say (‘plenty of other reason’), association isn’t causation.
I can absolutely see how a PHE (which is what I have) throttles output, it can only transfer what it can transfer, and is the throughout is less than that needed, then the system is throttled. But I am not sure that it necessarily impairs efficiency.
It does. I do not claim to be the world authority on PHE’s but if you read the public explanations of how they work, full efficiency running a HP across a PHE is physically impossible in the context of what we’re talking about – you can’t get the output hot to exactly the same temperature as the input hot. you can move all the heat energy, but it’ll always be degraded a bit on the output side. which must have cost you some efficiency in the HP.
whereas a straight piece of pipe doesn’t have any system loss just a tiny bit of thermal (but we’re assuming both systems are well insulated so that negates).
It gets harder to engineer, the smaller the DT, the bigger PHE you need. The issue with yours is more that its undersized. if it had been sized right we’d probably not be having this debate, the few % inefficiency would be a non-issue because your house would be warm.
I’m still sure about this, I think we might be mixing up throughput with efficiency. Consider the PHE as a form of obstruction: it restricts throughput. Even if the heat pump can produce 11kW, and the PHE can only throughput 8kW, then you have, in effect, my situation, with the heat pump reacting by only producing 8kW. A bit like trying to blow down a very small bore pipe. Your lungs can produce enough airflow to blow out candles six feet away, but the small bore pipe restricts the flow, and you only can only blow out one candle three feet away. But does that mean your lungs are now less efficient? Less capable, certainly, but less efficient? I can imagine something similar with a heat pump: its output is restricted, but it can still produce that lower output efficiently.
Nicely put.
and I am still sure also. we just need to be clear we are talking about the right things:
your system has a throughput problem, because of the undersized PHE.
because it has a PHE in it, it has an efficiency loss due to the temp drop across the PHE. Thats physics, it can’t not be there. But that isn’t your main issue because that problem is almost entirely masked by the first one.
Any system with a PHE (or llh, or buffer) in it will have problem #2. To varying levels depending on the quality of the engineering. In some systems its awful. In some , its acceptable.
An open loop system would also have a throughput problem if the pipes were too small and it wouldn’t work properly. that’d be equivalent to problem 1 above. But it would never have the “efficiency loss due to enforced temperature drop" problem (2).
I’m pretty sure this was Freedom. In effect, as I understand it, they supply an installation kit, and the installer installs what is in the kit. I’ve mentioned this before, I am pretty sure I asked my installer at installation time how the PHE was sized, and I think – it’s two years ago now – that his reply was Freedom supply a generic one, large enough to cover most installations.
I do wonder if part of the problem is that heat installation as done in this country seems to be largely done as a trade, and trades persons don’t as a rule get involved with serious (engineering) design, only basic stuff, which heat pumps definitely are not. This creates a vacuum into which suppliers can step: here’s our half day training course, we’ll have you up to speed in no time, we’ll even give you a kit of parts and an installation manual, and Bob’s your uncle. Add in a gutless toothless regulation system, and before you know it, we have what we have.
Again, it is back to the real world. Most car mechanics don’t have degrees in physics, and neither do most heat pump installers (so do, I know). It would take a huge effort to change that, and off the top of my head, right now I can’t see a way to do it.
Agree. Doubly so with retrofits, where system design in the context of the specific house is the key to an implementation which is effective, cost effective, and efficient. Of course there are good suppliers as well as good installers, but sadly not sufficient at present.
I don’t think you need a degree in physics (although it probably helps), but you do need engineering skills to do the system design and problem solving. Many plumbers are essentially fitters, very skilled at what they do but not able to do the engineering. Unfortunately the system engineering and problem solving associated with plumbing, which I think is inherently interesting, comes with the requirement to bend yourself double in a confined space, whilst being looked down upon by a sector of the British public. Not the greatest incentive for a bright young graduate.
An interesting assumption, to say the least! But lets suppose its true, you still have to question what they optimise for.
If there is a temperature drop flow-flow across the PHE/buffer/LLH it must impair system efficiency because it requires you to increase the flow temperature from the heat pump to achieve the necessary flow temp at the emitters. System efficiency drops with increased flow temperature, its in the thermodynamics and the manufacturers data tables.
agree. I’ve always thought a mandatory qualification for a plumber is to be wiry, with very strong but thin arms. had one once who was my build (flanker) and he always sent his scrum-half build apprentice into the tight spots. very skilled fitters as you say. But none of them was ever what I’d call a heating engineer, always at a loss when I wanted to discuss detailed system design . They would rely on vendor supplied information… which is where the likes of Freedom, Midsummer, Joule etc come in . The conjoining of it with the role of bathroom fitter doesn’t make for an interesting path for an technical graduate either.
digressing but I’ve pondered several times if there’s a way to combine my engineering/physics/system design skills with those of the young plumber down the road who is merrily servicing / fitting combi’s all day every day. can’t think of a way that actually works though.
It was a rhetorical question (? at the end), not an assumption!
Yes, I get that, but how large is that loss percentage-wise? The throttling effect reduces say 11kW to 8kW – a 27% reduction. I suspect the blockage is the main problem, not the agreed but possibly not very large drop in efficiency. Again, I am distinguishing between throughput on the one hand and efficiency on the other.
reposted because it got out of sequence somehow
As stated upthread about 2-3% per deg C, but if you want an accurate number check your systems data tables.
Throttling is a different phenomenon which may (will) in addition cause a further loss in efficiency because water is being recirculated through the heat pump without doing anything useful and you cant get owt for nowt. However I don’t have a figure for this effect and as you say its probably not the main downside of throttling.
Which is the point I was trying to make using lay language. The throttle effect (at 11 down to 8 kW) is around 27%, the efficiency losses are (much?) less. Taking @jamespa’s 2-3% per degrees C (between primary in and secondary out, I presume, which most of the time was between 1 and 2 degrees last time I took measurements) then the efficiency losses are say 2.5-5%.
This is the same as my blowing through a small bore pipe analogy. It is not a loss as such, or an efficiency question, but rather simply a failure to deliver.
I do get it, but in my non-physics trained mind I see two problems (as you do) but conceptualise them slightly differently: the first, and more important problem is an obstruction to flow, the second is efficiency losses that arise from the heat pump having to work harder to get the same water temp at the rads.
Still no reply from Freedom Heat Pumps on details of my PHE.
ok, we’re in violent agreement 🙂
amusing complete off topic… I happen to be Bass Trombone player in my leisure time. you can get a lot of energy down a small pipe if done right 😉
To some extent you are doing that by contributing to this forum. I have also wondered the same (but am enjoying being retired too much to want to commit at the present time). There are a couple pf people out there who are doing exactly that, albeit doing some plumbing as well, but trying to find ways to outsource this bit.
In general building we have Structural engineers, Architects and Builders. They manage to work together. The customer often contracts separately with them (for very good reason).
MCS mandates that your contract for the design and installation is with a single person (just saying!).
I think it’s called market forces, the efficiency of markets, or whatever those who work in the field that makes astrology look reputable call it these days. There’s nothing to stop firms that have an engineering department and a fitting department providing both sides of the equation – I’m not sure you really need the added complexity of multiple contracts – except that the engineering department is an unnecessary expense if Freedom et al are willing to step in provide a quasi-engineering department, in the form of their spreadsheet, along with their training, handy videos and installation kits.
I can’t think of another household or other purchase that requires potentially a lot of engineering input at the design stage, and then a considerable amount of fitting work to be done at the installation stage. Maybe the industry needs to think about new ways of working, though I have to add that in medicine any medical report that has new ways of working in the title usually means new ways of putting your feet up.
Really it’s system dependent, as we learn how few KWS we really need there are going to be proportionately bigger pipe layouts that the heat pump pump can’t cope with..1200 lph just won’t satisfy a system need 1800 lph
And it’s a brave person who poo poos system designs from manufacturers, and it’s cynical to think global manufacturers add things unnecessaryily. But I will grant you this, the very same manufacturers are doing a piss poor job educating installers and the public..
Hi Everyone,
It is strange how the same issues seem to pop up on the forum, it must be well over one year ago when CR and I were discussion the problem of having a PHE installed in his system, and my suggestion that he should consider having it removed.
@Derek M and all
We are at the getting to grips with quotes etc stage. When our extension is finished (and only then, and if we can face more disruption) in the spring we’re going for a ashp install. Neighbours have recommended their installer but looking at their web site (and our neighbours) they also install large buffer tanks (possibly piped as 4 port can’t recall, need to go round again) plus a llh for their ufh.
So how do you prevent an installer putting in all of the extra stuff, other than going with someone else.
I realise from this forum and others that an open system is best, with obvious essentials like having large enough emitters. I have used Heatpunk to size up our house and my results compare well with our gas bill, so know what is involved.
Similar question how do you stop the installer using the huge mcs defaults on leakage loss when our blower door rate are below 1ach?
You can try arguing with the installer. In my experience this will work with some, but many will take no notice. Basically its a sellers market so many don’t care about anyone who argues (in fact they probably actively want to discourage them). You will quickly find out which category any given installer fits into.
You can ask the manufacturer the specific question via their technical support line, and you may well get an answer or even a set of approved system diagrams. I found Vaillant, Mitsubishi, Grant, Cool Energy to be very helpful, Daikin pretty much said ‘ask your installer’ (even when I escalated) and Samsung haven’t responded to any technical query I have posed. One individual reported an extensive (and successful) conversation with Vaillant about some non standard requirements/simplifications that the installer had vetoed. Obviously if you can get answers from the OEM, the installer should listen.
You can read the installation/technical guides to see what they say and use that to challenge your installer.
Other than that its find another installer.
From memory – Mitsubishi, Daikin, Vaillant, Cool Energy, Midea dont. Samsung shows a buffer in an ‘example system diagram’ which includes just about everything under the sun (including a backup boiler – which is why the buffer is needed in that diagra,). I’m not sure they actually insist on one, its possible that this is ambiguous, which leaves it open to interpretation. Grant is a funny, I don’t think the manual for the underlying unit from Chofu does, but Grant then set out some installation guidance/requirements (basically install it as if it were a gas/oil boiler) – you will need to check how these are implemented in practice. I don’t know about Panasonic, Hitachi, Viesmann or sundry others, my front runners quickly came down to Mitsubishi, Samsung, Daikin or Vaillant.
In your situation I would be tempted to specify when asking for quotes that a quote with an LLH, Buffer or PHE in the primary will not be considered. That might put off those who otherwise will waste your time. I did similar.
Hi Judith, welcome to the forum.
I suppose that you could politely ask them to explain in great detail why there is a need for a buffer tank or low loss header, or anything else that you feel may be superfluous to requirements.
Similar question to all
i understand some ashp manufacturers insist on a llh/ 4 port buffer. Who are they so that they can be ignored, together with their installers?
I don’t see any aspects of “doing a bad thing”, LLH are a good engineering solution to some identified problems, namely emitter sizes (and hence total system volume) too low and on-off thermostats.
i hear people regularly say, “, I’m not changing my radiators” or “I love my Hive/Tado and I’m not parting with it”. In which case hydraulic separation is essential. Until the customer learns the cost/benefits.
Or the pricing system changes so like the Netherlands gas is more than electricity per kWh (by taxation). Not efficient use of resources though.
Sorry on my reading it does. I quote …
“So when you are in a low load condition you get this issue:… The flow slows down and the unit trips out on low flow alarm."
“In the really old days 2010-2013 we solved this with a bypass, if the flow dropped the bypass opened to allow a short circuit to maintain flow rate. It was OK but the installers refused to set it up correctly, quite rightly they thought the unit would cope. They were wrong."
…
“When I was a tech support engineers I got fed up with literally thousands of calls about low flow alarms so we made a solution. So in 2013 we decided to use a low loss header or plate heat exchanger to stop this problem, its a good solution but its expensive and it reduces system efficiency. But at least the unit runs without fault."
The first part says that there was a solution which didn’t compromise both performance and cost a lot, but installers wouldn’t use it.
The second part says that this forced them to adopt a different strategy even though they know it cost a lot and would compromise performance. Also it falls into the category of covering over the red light with a sticking plaster!
The strange thing for me is that even my gas boiler system has a bypass in it, so I struggle to understand why installers ‘wouldn’t set one up correctly’ with a heat pump.
Don’t misunderstand me, I fully understand why it was done, and its great that its out in the open. Its just disappointing that the reasoning has been less than transparent for so many years (so far as I can tell based on what I have read and what people say here and elsewhere), and that the practice still persists as ‘mandatory’ according to some.
Thats fair enough, as long as the cost of retaining it is declared. Customers should be able to make choices, and they should of course be informed ones. For the same reason I should be allowed to retain my vented 140l cylinder if I wish to, but most installers will absolutely insist on ripping it out.
Hi all – following this thread with interest if a little over my head at times…I took a look at my Daikin Altherma manuals (2020 install) and the attached show the recommendations for a set up with a single type of emitter (ie rads) and the set up for multiple emitter types (eg rads and UFH). I have the latter. They talk about the necessity for a ‘balancing bottle’ in this multiple emitter scenario. Not able to find much about ‘balancing bottles’ but it looks a bit in schematic like my (assumed) LLH. I run both my emitter type zones (rads and UFH) at the same temp under a WCC so the multiple temp set points is irrelevant to me. Are these ‘balancing bottles’ equivalent to a LLH?
@Marzipan71
In the diagram they look and are piped like a buffer tank (an LLH is, in effect, just a small buffer tank afaik). So far as I can tell from the schematics you posted the ‘balancing bottles’ appear only in the scenario where the are multiple types of emitter run at different flow temperatures
Thanks @JamesPa – the flow in the manual is a bit confusing but in Capture 3 Daikin seem to also recommend/ mandate a ‘balancing bottle’ in the scenario where an old gas or oil boiler is replaced with this particular Daikin HT model irrespective of whether there are different flow temps (I think – the Daikin manuals are not the clearest) – ‘When replacing an old gas or fuel oil boiler by a air to water heat pump system (EKHBRD*): please always check the specifications of the pump of the old unit [and] if the external static pressure of that pump is higher than the external static pressure of the air to water heat pump system, please install an additional pump with higher external static pressure in combination with a balancing bottle.’ I had to look up external static pressure which tells you where my level of understanding is.
Basically what this is saying is that, if the water pump contained within the heat pump isn’t strong enough for the job (because your heating system has too much resistance), then you will need a secondary pump.
I’m not actually a plumber, but I would have thought/hoped that there might be a way of putting another pump inline, without a buffer, to this job.
there is, but if you read up on pump curve hydraulics as I’ve been doing the last few weeks, the maths is painfully non linear. you need rapidly increasing head to get the job done, and the pump cost goes up rapidly the more head you need.
I was looking at my own single loop system, I get 28l/min from 8.9m of head on a 9.5m head pump (UPMM). 10kw at DT5 heats my house perfectly well, but my heat pump can take up to 42l/min and I’d like to improve performance where I can. If I was to put in a second identical 9.5m head pump, whether in parallel or in series, I’d gain as little as 1% flow rate, a pointless change of course. To get it done properly I’d need about 12m head which is one serious pump (e.g. UPMXL). £700 or so. so the answer in my case, time and money better spent on improving the pipework for a lower head loss – which I have a couple of places to go at, come the summer.
whereas the my system setup as a buffered split would almost certainly run fine with two 6m pumps or maybe 8m at most. cheaper mass market screwfix circulating pumps, much “safer" in that there would be no need to worry about flow rate for the installer. but less efficient.
The “Balancing bottle" in the above seems just another name for a buffer/LLH (not heard that name before).
It’s actually the same question I was asking the other day on the “new generation of HT heatpumps" thread. A new fangled HT heatpump is (to me) only an option for “straight boiler swap", if it can run at DT20 without having to worry about flow rate issues. (thats ignoring , for the point of this discussion only, all HT efficiency issues). If it needs DT5 same as any other heat pump we know and love/hate, then all the flow rate issues come right back, and so people start talking about adding a buffer/LLH to mitigate , and back round in a circle we go.
System volume problems are much better solved by installing a volumiser, which is similar to a buffer tank, but without the possibility of mixing and efficiency reduction.
Based on several conversations I’ve had this week, there is an indication that significant information may be released in February which could call into question the accuracy of heat pump manufacturing and efficiency data. If this turns out to be the case, it could lead to serious legal ramifications for both private companies and government entities.
Interesting. Is the research which led to this sponsored by the fossil fuel industry I wonder?
Obviously we all need the facts, but there is a big war going on here between the vested interests and the human race. I get the impression that the vested interests are beginning to get a little concerned.
@JamesPa, it is not the fossil fuel industry. To my understanding it’s a heat pump insider whistleblower. Wonder if it’ll be enough (or significant enough) to have an ITV drama next time this year.
Maybe not on a mainstream channel! Perhaps 5 minutes on rip-off Britain.
I confess I see the HT heat pump question is a bit of a side issue. The question really is, do ‘lt’ heat pumps have any advantages ove HT ones. The answer, so far as I am aware is yes, they are cheaper (for now – but I suspect its unlikely to last) and (if the HT is r290) have fewer placement constraints. But that’s about it. Unfortunately they tend also to be noisier and uglier as well as the refrigerant having a higher gwp, not because of anything to do with the temperature they are capable of reaching, just because manufacturers combine several developments in one go and don’t always retrofit improvements to earlier models. So far as I can assess they are no more efficient at any given OAT/LWT combination than HT ones.
So whilst I agree that aggressive marketing of ‘HT=straight boiler swap’ is misleading, it’s equally misleading to push LT pumps on the basis that running at HT is a bad idea. You don’t have to drive a car at 120mph just because it can reach that speed and nobody would rubbish a Porsche because it can (but is not forced to) be driven at well above the legal speed limit!
As it happens I am more or less certain to end up with an HT pump, running at 45C, because there isn’t an ‘LT’ pump which fits the physical, aesthetic and noise requirements. Is there any reason to suppose ‘LT’ pumps will exist at all in say 5 years?
At the risk of being drummed out for heretical thoughts ( ;-))) ) No, I’m sure I wouldn’t be, … would I?! Suppose this LLH is losing some efficiency – where is the loss taken place and where is the wasted energy going please? If the loss is in the form of heat that doesn’t make it across the interior of the LLH, does it radiate into the surrounding area? In my case, this will be the airing cupboard where such heat will be ‘always useful’, (harking back to the topic of uninsulated pipe runs within the home again!). If the unharnessed energy is being deflected back out into the return pipe-run to the heat pump outside, I can see that this might well be wasted heat though. Regards, Toodles.
The principal reason that LLH reduces efficiency is if there is a temperature drop flow to flow across it (which there almost inevitably is unless it is particularly well set up). This means that the heat pump operates less efficiently, because it must operate at a higher flow temperature to achieve the same temperature at the emitters. Part of the reduction in efficiency will be that the compressor (which is usually outside) has to work harder, and part of the loss will be that not as much energy is extracted from the outside air. So no, the ‘lost’ efficiency does not result in an increased radiation into the house (nor is it the case that a ‘loss’ of energy takes place in the LLH, albeit that it is the cause of the reduced efficiency – the reduction in efficiency occurs even if the LLH is lossless)
There will also of course be some actual loss of energy from the system at the LLH, due to convection. Depending on the location of the LLH that might get radiated into the house. This can be ignored if the LLH is within the heated envelope, and generally is ignored in these discussions.
If you have any more heretical thoughts then please let me know, so that I can send the Inquisitor round. 😋
The loss isn’t actual thermal energy as such, the loss is due to reduced efficiency (lower COP). Because of possible temperature reduction from primary circuit to secondary circuit, the LWT may have to be higher to ensure the heat emitters receive the required quantity of thermal energy.
To produce a higher LWT the compressor has to work harder, using more electrical energy, and in turn the heat pump absorbs less free energy from the OAT.
The overall thermal energy supply to the home should be approximately the same, just less free energy and more expensive energy.
@Derek M Just for ‘fun’, I placed strips of matt black insulting tape on the four pipes to and from the LLH and used my IR thermometer to obtain these approximate readings; I measured the four points a number of times to attempt to obtain steady readings and my best attempts tend to suggest the following temperatures.
Input to LLH from heat pump: 29.8 deg. C
Output to emitters: 29.0 deg. C
Return from emitters: 28.0 deg. C
Return to heat pump: 28.8 deg. C
Do these readings look as if they may be true? I’ll take another set of readings another day when time permits (don’t get older if you can help it, you spend more time than you might like draining the NHS facilities!) meanwhile without placing ‘proper’ sensors on the pipes, I’m not sure I can increase the accuracy. I wonder if there is also room to improve the Delta T by adjusting the secondary pump? Regards, Toodles.
I can’t remember ever having used an IR thermometer, but then I’ve always had access to what I would term correct test equipment. I do believe that one of the other forum members found difficulty getting accurate readings using an IR thermometer. What is the specified operating range and tolerance?
The actual readings obtained could be appropriate for a mild day like today, but again without other values to compare it is difficult to know for certain.
The DT does look low, but again without comparing with values measured during colder weather conditions, I cannot say for certain.
Without further data, I would suggest that you just monitor, without making changes, especially if you are warm and it is not costing you an arm and a leg to operate.
I keep advising people not to grow older, but they will insist upon doing so. 🙄
@Toodles I’ve tried IR with black tape, doesn’t work very well . Other forum members have had good results for very little spend with a set of these from amazon. tape them tightly to the pipes, pipe insulation over the top to isolate from ambient.
@iancalderbank Oh Ian, I couldn’t see a link or any product details – please could you detail the goods again? My current attempts have been with a non-contact IR Thermometer with a spec. Of 0 ~ 550 C. +/- 1.5 %. Probably indicative but the tape covered pipe might be causing all sorts of errors I would imagine. Regards, Toodles.
@Derek M The system seems to be working well, we are warm and at approx. 450-500 W/h in this present warm weather, I feel all is goodness and light. (COP shows as 4.5 plus), when it was – 6 or -7, the COP was approx. 2.6 I think. As Ian has mentioned, an alternative means of measuring the actual LLH adjoining pipe temperatures would be better though. Regards, Toodles.
@Toodles I put a link in the word “these" in the previous post. this type of thing. others on here have used them successfully.
@iancalderbank Thank you Ian, Regards, Toodles.
@iancalderbank Amazon delivered the four thermometers today; shame that there was not insulating material interposed between the contact and the button cells; flat cells in three of them and a faint glow only from the other! Did extended battle with Amazon help line / suppliers site and now await replacements. Ho-hum more grey hairs (well, actually, they are white already) and time I won’t get back!;-) Regards, Toodles.
@Toodles You were unlucky. I got the same 4 digital sensors over a year ago and all batteries are still going strong. Great devices across the low loss header to check primary and secondary flow and return temperatures. Make sure the sensor is touching the pipe and well insulated. Cable tie sensor to pipe, and then cable tie insulation completely over it. They would probably benefit from heat sink compound, but my memory of that stuff from my apprenticeship days is it ruins clothes instantly!
@AllyFish I had a reply from the supplier, requesting a photo or video the the product!!! I sent a phot of the four displays; one was readable, one was feint and the other two were blank. I asked if they didn’t trust me? Anyhow, I orderedmsome LR44’s that should arrive today so that I can put the ‘kit’ together. Perhaps the supplier will send me another 4 units, I doubt they sell the cells anyway! Regards, Toodles.
I purchased some LR44 button Cells and powered up the 4 sensors; I laid the four probes close together and placed a Govee thermometer on either side of this bundle of sensors. The Govees both indicated the same temperature and I left the whole caboodle for 5 days occasionally comparing the readings on all four sensors to the Govees. I found that two of the sensors were consistently 0.1 degree C low and 0.1 degree C high and the others were 0.9 and 1.1 degrees C lower than the Govees. The four displays were then taped into a little ‘block’ and the probes taped onto the LLH pipes and covered with insulation. I left the probes to settle for an hour and then read (as per the photo) the results. Top left and bottom left are the heat pump flow and return; the top right and bottom right are the flow from LLH to emitters and return respectively. The left hand displays are both within 0.1 degree of Govee reference and the right hand pair are 0.9 and 1.1 degrees of reference. Outside temperature (according to Daikin Onecta app) was 13 degrees C and heat pump and secondary pump are noth working. Any comments welcomed but I’ll see what results show when OAT becomes more winter-like. (One other thing, supplier has not supplied replacement button cells so have reported them to Amazon) Regards,, Toodles.
@Toodles
So applying the correction factors which you have established, the LWT is 37C and the RWT is 34.8C, giving a DT of 2.2C in the primary circuit. On the secondary side of the LLH the flow temperature is 36.7C and the return temperature is 34.5C, again indicating a DT of 2.2C.
The temperature drop across the LLH is only 0.3C, so I would assess that your system is operating in quite an efficient manner.
@Derek M 😊 Toodles.
@Derek M Hello Derek, I have left the system running with the thermometers in place for a few weeks now; glancing at the readings from time to time indicates that the varying OAT’s for a constant IAT show that the differential is fairly consistent. The displays are: Top Left = Flow to LLH. Top right = LLH flow out to rads, Bottom right = Return from Rads and Bottom Left = Return from LLH to ASHP. With the correction factors of the two right hand displays being 1 degree C. lower when all sensors were bunched together for several days, I am applying a +1 degree to these two thermometer readings; though I know these are not super-accurate devices, I think they probably provide a reasonable indication of the trends of changing temperature at the 4 points. I seem to have an average drop of 0.2 – 0.3 degrees across the input from the flow to the output of the LLH and 0.3 – 0.6 degrees C. across the return to the LLH and the return to the ASHP.
From time to time, I notice a dynamic ‘blip’ from time to time where one display or the other might indicate perhaps a 1 degree difference but this is short lived usually. I even noticed a difference of 4 degrees momentarily where the flow into the LLH exceeded the reading on the flow out to the rads; this lasted about 30 seconds or so and I have no idea why this should happen.
I don’t know the make of LLH as no label is visible but it is approx. 46 cm. Tall and 17 cm. wide.
Observations welcomed please!. Regards, Toodles.
I suspect that the image was subjected to some filesize reduction so here is a close up of the displays. Toodles.
I believe that the temperature readings indicate that your system is quite well balanced, in that the flowrate into the LLH is slightly greater than the flowrate out to the radiators.
This is probably the optimum achievable situation, since the slight mixing that is taking place within the LLH is at the return flow end. Slight mixing of the return flow should not have a detrimental effect on heat pump operation and overall efficiency.
Thank you Derek, at least it is only a little ‘Devil’ then! Regards, Toodles.
Many of you may be aware of my growing skepticism towards certain elements of the heat pump, and one aspect I find particularly perplexing is the position held by both manufacturers and installers of heat pumps. This confusion was further compounded following my participation in an online discussion involving a group of installers and a representative from one of the leading heat pump manufacturers. The debate quickly escalated, especially around the topic of buffer tanks, reaching a point of intense contention. Interestingly, the manufacturer chose to remain notably silent as the installers, who were divided in their opinions, engaged in a heated exchange.
The crux of the debate revolved around whether buffer tanks could be installed efficiently and effectively by installers in general. The conversation revealed that integrating a buffer tank with a low temperature heat pump system, along with managing all related components, is a complex process. It became evident that a significant number of installers in the UK lack the necessary skills and training to execute such an installation successfully. Prompted by this realisation, I questioned why the industry doesn’t move away from using buffer tanks altogether to avoid the complications associated with their installation.
This query led to an unexpected direct message from a high-ranking official within the manufacturing company, asserting their unequivocal support for the use of buffer tanks and their desire for these components to be incorporated into installations, regardless of the efficiency of the installation process. Needless to say, this was a private exchange, and a position they didn’t want to express publicly.
This admission was startling and left me perplexed about the overarching objectives of the heat pump industry. It begs the question: why are we installing advanced heat pump systems only to undermine their performance with suboptimal installations? Surely, the ultimate aim should be to ensure that we are installing the most efficient systems possible, rather than settling for setups that significantly impede their functionality.
@Mars Mars, as you might know, we have an LLH (which fortunately seems to be running with relatively low losses to the efficiency 😉). I am not about to rip out the LLH to extract a little more efficiency though! The majority of installers seem to opt for an LLH or a Buffer Tank by default as a ‘rear covering’ exercise don’t they? I had a long conversation with the director of the installers and he seemed to view the situation as a positive addition as it removed the necessity to achieve such a delicate setting of the Delta T performance from the secondary circuit that fed the emitters. I think our system is running well, but there is always the nagging feeling …’Might my Air Source Heat Pump run more efficiently if I had the LLH removed?’ Regards, Toodles.
The cynic in me says this is about reducing call-outs & guaranteeing adequate volume for defrost. From a customer POV, as well as having the potential to be poorly installed, a buffer increases cost and takes up space which many may not have.
It would be worth, IMHO, pressing them on the question of whether they mean ‘buffer tank’ or ‘volumiser’. The latter at least has less potential for poor installation.
Is there also a danger in the terminology that is being used ie low loss header, buffer and volumiser. Not all LLH’s act as buffers, correctly specified and installed they operate perfectly correctly as a hydraulic separator. It very much depends on where on the LLH the ports are positioned.
Are we in danger of vilifying an entire class of products?
As far as I am aware there would be no problem with a LLH or buffer tank, if the primary and secondary flowrates can be balanced to ensure that no mixing of the flow and return takes place. Obviously balancing the flowrates becomes problematic if the heat pump controller is able to vary the primary flowrate, without the necessary adjustment also being performed on the secondary, thereby unbalancing the system.
Having an additional water pump that may not be necessary is also a possible waste of electrical energy.
True, but it appears they are frequently not balanced.
My questions to @Abernyte (or anyone else) is:
In a domestic installation of a ‘normal’ scale (say up to 6 bedrooms/300 sq m) with either radiators or UFH but not both
what value does a LLH add?
what value does a buffer add that a volumiser doesn’t add?
The application of Occams razor is generally a good principle so until we identify the value add then there is no argument for their presence.
Agreed
Surely an LLH suffers from mixing of flow and return to the same extent, probably more because its smaller, than a buffer does, and like a buffer needs to be set up properly to function without degrading efficiency (which seems to be where many installations go wrong).
Can you explain why ‘hydraulic separation’ is needed in a typical domestic central heating system. I totally understand why extra volume may be needed, but not hydraulic separation. if you are doing something complex with a back up boiler or a rather large system then maybe, but in a typical house what value does it add?
The default setup on a Mitisubishi Ecodan solar thermal ported pre plumbed cylinder has a LLH. My installer, who was one of the highly experienced “better" class of installer when queried regarding this said that the LLH in question has the flow injection plume above the return fitting outlet (not opposite as some seem to have) and as such would operate as a thermal separator to allow the primary and secondary pumps to operate efficiently at different variable speeds.
Since installation the system operates with a flow temp rarely above 35C and has been a resounding success as a heating system. Not a scientific recommendation I admit but I see no reason to doubt his explanation …so far!
Which simply begs the question – why do I want primary and secondary pumps in the first place (which incidentally must be balanced for the LLH to work without impeding system efficiency). For the avoidance of doubt I’m talking about a typical fairly simple domestic setup where a heat pump replaces a gas boiler (ie 95% plus of real world scenarios). Why would I have a second pump, a low loss header/buffer etc. None of this appears in your typical CH system. What value do they add.
You may not know I accept, but until someone tells us then the best assumption is no value at all and, since they clearly add trouble and cost, thats a good argument to leave them out.
@Abernyte I suspect that arrangement might be similar to the one in our airing cupboard. The flow is the top left pipe and the return is the lower left. The top right is the flow to the secondary pump thence to radiators and the lower right is return from the radiators? Regards, Toodles.
Yes other than Mitsubishi use a 35mm LLH
But why (bother with a secondary pump and llh) in a typical domestic install?
Does anyone actually know a reason that stands up to scrutiny? I am not trying to be difficult, I genuinely want to know? @Abernyte, @Mars, @Derek M any ideas or is this another appendix from heat pump history that needs to be surgically removed?
The only reason of which I can think, is that it would be to allow system designers to accommodate ‘smart’ thermostats and TRV’s into their designs, without suffering ‘low flow’ problems.
Wow that’s inventive but I’m sure you agree that it can be discarded as a legitimate reason.
Perhaps we ought to ask why should they be included rather than trying to argue that they should be omitted. No system designer worth their salt includes components without a reason.
Which is why I have spent the past three years trying to convince forum members that they should have their poorly designed systems corrected to make them operate more efficiently.
I think you are both correct, its because systems aren’t designed, they are plumbed in by people who don’t understand system design but attend a manufacturer’s installation course. So the additions of these components are their to mitigate any system design and it will function in any given scenario, not optimally but it will function.
I fear you are right. However the reason suggested (which is very plausible) is the equivalent of dressing a dirty wound instead of first cleaning it up because the patient complains about the sting of the antiseptic, except that if you did the latter you would likely get struck off.
Naive input here:
I understand that LLH are supposed to act as impedance transformers (when set up right), giving the option of a higher delta T across the radiators in the secondary circuit. Hence the pump requires a dT of 5C but that isn’t enough to give enough heat output from the radiators. So for the considerable proportion of potential users who don’t want very big radiators (or any changed) then the LLH allows a larger dT say 10-15C and the colder water is mixed back in the return path.
This requires a higher flow in the primary circuit than the secondary afaik and everything set up right.
I only know what I’ve read, I’ve not installed or designed an ASHP system.
Clearly for the customer preference of not changing radiators there is a potentially much higher installation and component cost and ongoing consumption cost.
Please don’t trash me if I’ve misunderstood what I’ve been reading.
The quantity of thermal energy that can be emitted from a radiator is primarily dependent upon the Average Water Temperature (AWT) within the radiator the Indoor Air Temperature (IAT), and the standard heating capacity for the size and type of radiator, which is normally specified at DT50.
So if the Leaving Water Temperature from a heat pump going into a radiator was say 45C and the Return Water Temperature from a radiator was 40C, then the AWT would be approximately 42.5C.
A single panel type 11 radiator of size 1200mm x 600mm has a specified DT50 of 1141W, while a double panel type 22 radiator of the same size has a specified DT50 of 2051W, almost double the thermal energy output.
If a LLH is installed between the heat pump and the radiator, the maximum temperature of the water entering the radiator can be no greater than the LWT from the heat pump, so the only way to increase the DT across the radiator would be to reduce the secondary flow rate so that the water spends more time passing through the radiator. The net effect would be to actually reduce the thermal energy output of the radiator, since the AWT would also be reduced. If the flow temperature going into the radiator is 45C, but the return temperature coming out of the radiator is 35C, giving a DT of 10C, the AWT will now be 40C, not 42.5C.
I have attached a radiator heat output calculator which can be used to estimate the thermal energy output of different size and type of radiators under different operating conditions. The yellow highlighted cells can be varied with the results appearing in the green highlighted cells.
@Judith
Derek has explained it technically, just to add for the avoidance of doubt – it simply is not true to suggest that adding a LLH can overcome a requirement (if it exists) to upsize radiators when switching to a HP. If someone told you this then they were either deliberately deceiving you or didn’t understand it themselves, or both. However it’s easy to see why the misunderstanding could occur so you don’t need to feel bad about it!
The only circumstance I can think of where some form of ‘tweaking’ of deltaT at the emitters might overcome the need (if it exists) to upsize radiators is where the required upsizing is very marginal. If you can run the secondary circuit very fast, the deltaT across the emitters reduces, in the limit to near zero. This will increase the average temperature of the emitters by no more than 2.5C, which will increase their heat output by about 15% at a typical flow temperature of 45C. I cant actually work out if, or whether, you could get this to work in practice, because it implies that the deltaT at the heat pump is also near zero (and thus the rate of flow must also be fast). The heat pump may, or may not, be OK with this. You are going to get a lot of noise from your CH system if you attempt this, and pipe erosion, so Im not suggesting that its a sensible idea, just that it doesn’t immediately violate the laws of thermodynamics.
@Derek M and others
i think I’m getting there, so can I try this out…..?
There are too many dTs in this game. Derek rightly corrected me on average flow temp through the rads, so to get back up to the same average flow temp the input flow temp (LWT) has to be increased. Hence one of the sources of inefficiency in the ashp/llh combination
BUT on a boiler system with a higher LW temp say 60C the dT across the rad is a smaller proportion of the dT to the room (thus showing too many dT!😉) and anyway with a boiler the LWT -efficiency curve is not as severe.
Does this make sense?
Users should never hesitate to ask questions on our forums – this isn’t Facebook 😉
Pretty much but worth unpacking for absolute clarity
Yes!
Exactly, Heat loss from rad to room is dependent on average flow temp through the rads. The DT across the rads will be driven by this and flow rate not the other way round.
If there is a reduction in flow temperature (flow to flow) across the LLH then yes. If the LLH is perfectly set up the reduction in flow temperature will be small, so possibly no material inefficiency. But frequently it isnt perfectly set up and anyway, in the absence of a concrete reason (and in most domestic setups there isnt a concrete reason), why bother with the LLH because it costs money and is the source of problems.
The key is that LWT (and thus the average emitter temperature) is higher, although in a modern system possibly not by that much, if at all. The latest BRs require the design to be at FT=55. If you persist with the typical 20C deltaT flow to return, the average rad temp will actually be 40C, a bit lower than the 45/5/40 combination used frequently for an ASHP, but in practice essentially the same.
However typical practice until recently (and I suspect still in the vast majority of cases) is to set (or rather leave) a boiler FT at ~75 which does lead to higher average rad temp. Actually this very likely also causes quite a severe efficiency hit because its entirely possible/likely that the boiler wont condense because the return temp is too high – you can tell because a boiler that isnt condensing will have plumes of water vapour emitted from the flue – which you see all the time! Thats worth, I believe, ~10%. However almost nobody takes any notice of the efficiency of gas powered central heating systems. One might, very cynically, argue that the market actively distracts them from doing so by providing lots of ‘controls’ with various degrees of smartness that purport to improve efficiency but may not do so by anything like as much as we are led to believe.
Just like an ASHP, one of the best tips for getting greatest efficiency (and comfort) from a gas boiler is to turn down the flow temperature to as low as you can consistent with the house being sufficiently warm!
@Mars
Heat Pumps …………Short Cycling
Older Heat Pumps
1) In all older Heat Pumps the Power was controlled and regulated by binary state , ON-OFF Cycling.
Modern Heat Pumps
2) In Modern Heat Pumps the Power is Continuously controlled by an inverter.
3) Modern Heat pumps revert to binary state Cycling when the power required drops below a Minimum Value.
4) Cycling will be more apparent when the required power is at a minimum during Spring and Autumn.
5) Cycling can, however, appear at any time of the year on any Heat Pump.
Cycling time
6) When an Inverter Power Controlled Heat Pump is operating below the minimum Inverter Power the Heat Pump is cycling.
7) The time taken during cycling is made up from a positive ON Time Pulse or Run Time followed by a negative OFF Time .
Run Time
8) The positive ON TIME,( RUN TIME ) period is determined by the time taken to heat the Volume of Water within the pipe system to a set Temperature.
OFF Time
9) The Negative OFF TIME period is the time taken for the Pipe Water Temperature to fall to the required pipe Water Temperature.
10) The pipe Water Temperature is determined by a Thermostat.
Cycle Time
11) The Total Cycle Time = Run_TIME + OFF TIME.
Pipe Water Volume ?
12) The Cycle Period is determined by the Volume of Water within the Pipes.
MCS Calculation of the Volume of a Buffer Tank?
Please see the Explanation , given by the MCS into the Required Buffer Tank Volume .
Conclusions
A) Buffer TANKS MAY, SOMETIMES, be Necessary !
B) Buffer Tanks come at a potential cost !
ian
As far as I am aware short cycling can be cured just as effectively by a volumiser as opposed to a buffer tank. Volumisers dont depend on accurate control/setup, they are just passive. @Mars, @iantelescope, @Derek M . Am I wrong?
I can see that buffer tanks may be required if you want to combine two heat sources simultaneously (if its either/or zone valves will suffice.
If my understanding is correct, volumisers and buffer tanks may be primarily required to help with the defrost cycle. Once this additional volume of water has been brought up to temperature I believe that it will have little effect in reducing cycling (short or otherwise).
Think about what is happening. The heat pump initially supplies thermal energy to heat up the additional volume of water contained within a volumiser or buffer tank, but this volume of water will not emit much thermal energy during the heat pump off period, so no longer present a heat demand when the heat pump restarts.
I believe the location of the LWT and RWT sensors is the more important factor, since they are the devices affecting when the heat pump starts and stops.
If the LWT and RWT sensors are located in the heat pump unit outside, then it is likely that they will cool down much quicker than if they are located within the thermal envelope of the home.
My own home heating system has a temperature sensor located on one of the radiators, which in conjunction with the controller, initiates the starting and stopping of our heating system. This varies the frequency of operation from approximately 4 times per hour during sub-zero weather conditions to once every 2 or 3 hours when the weather is milder.
Doesn’t the effect on cycling depend on how the water pump is controlled. If the pump (secondary in the case of a buffer tank, only in the case of a volumiser) continues to operate after the heat pump has switched off then the volumiser/buffer tank will cool and the energy will be given up to the house. This will increase the period of the cycles but of course wont and cant change the mark-space ratio. If on the other hand the water pump switches off when the heat pump switches off, then I agree with what you say.
My comment above still broadly stands, but in extended fashion given yours ie:
As far as I am aware short cycling/lack of stored energy for defrost can be mitigated just as effectively by a volumiser as opposed to a buffer tank (with appropriate water pump control). Volumisers dont depend on accurate control/setup, they are just passive. @Mars, @iantelescope, @derek-m . Am I wrong?
@Mars
All Modern Heat Pumps will Cycle when operating BELOW the Minimum Inverter Power .
Here is a detailed graph of the Power my Heat Pump consumed during the evening of 23-March-24.
The Cycling Time, Run_Time ( Mark *) + OFF_Time ( Space *) = ~ 10.12 Minutes.
Here is a more detailed Graph of the Power consumed during the evening of 23-March-24, showing the Run Times.
The instantaneous RUN Time is , here, ~5.0 Minutes.
Here is the FFT of the Power consumed during the evening of the 23-March-24 , showing the Cycling Frequency.
The Frequency Maximum , here provides an Average Cycling Time of 9.96 Minutes.
The First Harmonic of the Cycling Frequency provides a Check, giving a 5.03 Minutes.
The RUN TIME CALCULATION **
My Heat Pump has a 50 Litre Buffer Tank fitted Across the output ports of my Heat Pump.
When Operating Below the Minimum Inverter Power of 2.5 Kw my Heat Pump is Cycling.
The Energy input into the Buffer Tank , when operating at the Inverter Minimum Power , kWh = Minimum_Power ( kW ) X Run_Time (Seconds)
The Energy Input Heats 56 Litres of Water to the Temperature Difference Across the Buffer, Delta_T .
The Energy Required to Heat 56 Litres of water to a Temperature of Delta_T is:
Energy Required to Heat 56 Litres of Water to ~4C = 4.18 X 50 X 4
Therefore, the 2.5 kW Minimum Power X Run_Time = 4.18 X 50 X 4
Therefore, Run _Time ( Seconds ) = (4.18 X50 X 4 ) /2.5 Seconds.
OR
Run_Time = (4.18 X 50 X 4 ) /(2.5 X 60 ) Minutes.
My Calculated Run_Time is Therefore , 5.57 Minutes
My Instantaneous Measured Run Time is ~5.00 Minutes.
My Average Cycle Time ( from FFT ) is 9.96 Minutes.
My Average Run_Time ( from FFT ) is 5.03 Minutes.
Is my Heat Pump STILL Short Cycling ?
* Sorry to use the Electrical Mark to Space Ratio Terminology
** Check the MCS Calculations in :
@Mars
All Modern Heat Pumps use an Inverter to control Heat Pump Water Power.
All modern Heat Pumps have a Minimum Power BELOW which the HEAT PUMP WILL REVERT to Cycling.
The DECC, in 2012, produced a Report on the Effects of Cycling on the Heat Pump COP:
The DECC Report was produced at a time when Heat Pumps with Inverter Power control were in their infancy.
The Report is however still useful when operating an Inverter Heat Pump BELOW it’s Minimum Inverter Power.
The Reports Recommendations are shown in the following :
Recommendations:
1) Recommended that Air Sourced Heat Pumps should be designed for a Minimum Run Time of 6 Minutes.
2) Run Times of ~ 8 Minutes gave COP Values close to the “Catalogue" Steady State Values.
3) 4 Pipe Buffer Tanks show a promising method of achieving the required Minimum Run Times without the need for “Excessive Buffer Volumes".
The Buffer here used was a Buffer fitted Across the Output ports of the Heat Pump :
Note also the Calculation of the Size of Buffer required:
Further note that these calculations are for an older control system, but , none the less valuable in the demonstration of a Buffer Tank fitted Across the Heat Pump Water output.
Also note the , by present standards, Very Poor COP that were achieved.
ian
@JamesPa
You are indeed correct, it may depend upon what the water pump(s) are doing.
I know that some of the heat pump controllers continue to run the water pump for a number of minutes after the compressor and fan(s) have stopped, and may also periodically operate the water pump for several minutes to equalise the water temperature around the heating system.
From observing my own heating system, it takes approximately 4 minutes to heat the radiators to the temperature calculated by the controller, after which the boiler and water pump is stopped. During colder weather conditions the required radiator temperature may be in the 40C to 45C range, and it may only take 10 to 15 minutes for the radiator temperature to reduce by approximately 5C, at which point the boiler and water pump is restarted. During milder weather conditions the radiator temperature may only need to be in the 30C to 35C, so it may then take 30 to 60 minutes for the radiators to cool sufficiently for the boiler and water pump to be restarted.This keeps the IAT at 21C +/- 0.2C under all conditions.
The point I was trying to make is that the location of the LWT and RWT sensors is very important, particularly if the water pump(s) do not run continuously when the heat pump is no longer producing thermal energy. Continuously operating the water pump to prevent the LWT and RWT sensors cooling too quickly probably would reduce the cycling frequency, but would use more electrical energy and may also transfer thermal energy from indoor to outside. I’m not certain if any controllers operate in this manner. It would be interesting to see how the different heat pumps control their water pumps and also the actual location of the LWT and RWT sensors, and the effect this may have upon the frequency at which cycling takes place.
As I have stated previously, one possible way to reduce cycling frequency could be to set the WC curve such that it causes the IAT to start to increase before the heat pump reaches the point when frequent cycling is likely to occur, and then use a room thermostat to start and stop the heat pump rather than the LWT and RWT sensors.
@Derek M The carel controller in my ASHP allows me to specify three pump modes: Normal, Demand, Continuous…
Normal – pump shuts off when setpoint is reached. Use this when driving a buffer tank.
Demand – pump will ‘sniff’ for a bit to see if the water in the circuit has dropped below the setpoint. No idea when you’d use this mode.
Continuous – pump runs whenever the call-for-heat is active. Compressor/fan come on as required under the control of the PID in the heat pump.
I use mine in continuous mode as I only have the single pump and I don’t have room stats.
As stated upthread about 2-3% per deg C, but if you want an accurate number check your systems data tables.
Throttling is a different phenomenon which may (will) cause a further loss in efficiency also because water is being recirculated through the heat pump without doing anything useful and you cant get owt for nowt. However I dont have a figure for this effect.
I’m sure that is absolutely right!
@Mars
Design & Measurements of Heat Pump Performance?
Wall Thermal Conductivity, U ……………abuse ?
Given my own experience, where my “installer" Altered the Wall Thermal Conductivity to justify the use of a particular Heat Pump Can I again ask the Question :
Why are Thermal Wall Heat Conductivities NOT Measured ?
Measurement would require the use of a standard Electric Fire attached to a Power Meter with TWO Thermometers , One indoor, the other Out Side.
From Experience, measuring U is far more accurate and Untainted by installer behaviour.
Measurement of the Performance of Heat Pumps?
Heat Pump Performance should be measured with an in -Water Power Meter !
Heat Pump Performance , COP should be Measured at the Start of the Piping System AND NOT at the Heat Pump itself.
Design
Heat Pump Systems should be designed with a Thermal Software e.g. H2x .
Measurements against the design?
Having completed a Software design the Performance MUST be tested against the Design!
Any deviations between the Design and Performance will bolster customer Confidence.
ian
p.s. As William Thomson, Lord Kelvin , said " if ye canny Measure it …..ye don’t understand it"
My Heat pump REAL COP ( that measured at the start of the Radiator pipe circuit ) and Heat Pump COP ( as shown by the Heat Pump itself ) are for 28/29 March:
My REAL COP is therefore , circa 2.2 , while my Heat Pump COP is circa 2.9.
The Difference between My REAL COP and the Heat Pump COP is reflected in the Energy loss between the Heat Pump and my house:
The Average Loss is therefore circa 26% without using the HOT WATER TANK.
“Short Cycling" is shown in the FFT of the Heat Pump Power consumption :
With the Peak representing a Cycle Time of circa 10.11 minutes.
Peak Frequency = 157 Hz on a run of 95274 Seconds duration gives a Wavelength of ~95274/157 Seconds , or ~10.11 Minutes.
The Run Time is shown in the following :
With the RUN Time here of 4.5 Minutes.
Conclusions:
1) With the DECC Report recommending a Minimum 6 Minute RUN TIME My Heat Pump is “SHORT CYCLING".
2) With the DECC Report recommending a Minimum 16 Minute CYCLE TIME My Heat Pump is “SHORT CYCLING".
Measuring Cycle and Run Times on a Heat Pump
I record the Power Consumed by my Heat Pump on a Daily basis.
For example , on 30 th March I get:
Clearly, my Heat Pump is suffering from “Short Cycling". The Question is “How Much"?
I can examine the “Short Cycling by taking the Fast Fourier Transform :
But , again , the “Short Cycling " , although much more prominent , with a peak at ~150 Hz , is still very Noisy!.
Also, the Run Time component of the cycle time is completely lost in the Noise!
Using the FFT as a filter for the Cycle Time gives:
Now a beautiful Noise free Sinusoid giving the exact Cycling Time as 10.12 Minutes!
On using the FFT as a filter for the RUN TIME :
Again a Beautiful Noise free Sinusoid giving the exact RUN TIME as 4.3 Minutes.
All Graphical work was performed using “SCILAB " on a LINUX PC.
Many congratulations to “Dassault " in France for rebuilding Scilab after a absence of Three Years!
Scilab will , probably work on “Windows" , probably!
Is my Heat Pump Too SMALL for Winter AND TOO BIG for Spring?
My Heat Pump does Not supply ENOUGH Power HEAT DURING Winter .
Notice the HEAT PUMP is permanently ON , Controlled by the Inverter.
My Heat Pump does Supplies TOO MUCH Power IN Spring!.
Notice the HEAT PUMP is “Short Cycling" , Controlled under Cycling !.
The RANGE of the Inverter , between Minimum Inverter Control and Maximum Inverter Power is TOO SMALL!
The Solution Would be to provide a Backup Electric Immersion Heater inside my Volumiser Tank.
Why Do Manufacturers NOT Provide the MINIMUM AND MAXIMUM INVERTER POWER?
Heat Pumps: Hypothermia & Bankruptcy
Having spent ~£14k on a Heat Pump I am now , a 76 year old , Am I Now faced with Heat Pump Hypothermia ?:
My “Installer" has now been STUCK-OFF for the THIRD TIME with the NIC making the comment that
" YOU ARE NOT GOING TO LIKE THIS ……………………BUT NOTHING CAN BE DONE “
The NIC have said that they are “Sorry" but that they have exhausted their efforts by the application of Further SANCTIONS against my “installer".
My Blood pressure is , on average, over the Winter 155/84 as shown in the following graph:
I am paying ~£165 per month for the running costs of this Heat Pump !.
I am paying ~£42 per month for the “loan " repayment for a “Drawdown " Payment for this Heat Pump!
Heat Pumps: Hypothermia & Bankruptcy
Frenchmen, Germans and Blushing Heat Pump “Engineers!"
Over the past two years, visiting “Engineers" have produced the most extraordinary comments .
A visiting French Samsung “Engineer" produced the following classic:
“Only the Germans REALLY Understand How Heat Pumps work!"
A visiting Blushed to the roots of his hair saying to his colleague :
" Perhaps you cannot set the Water Temperature because of what is being displayed on the Front Screen !"
The Blushing “Engineer" had previously been found to have falsified my house Energy requirements to justify the installation of the wrong heat Pump.
Another “Engineer" said that :
“WE will Repair and , if necessary replace your Heat Pump IF YOU AGREE TO THE REMOVAL OF ALL METERING". I Declined the offer.
A visiting NIC “Engineer" said that “I , the user, should NOT INTERFERE WITH THE SETTINGS INSTALLED BY MY INSTALLER “.
A Visiting TRIO OF ENGINEERS , including a NIC Engineer succeeded in completely stopping my Heat Pump when trying to simultaneously set the Water Temperature using “Weather Compensation " AND Explicitly set the water Temperature using the Heat PUMP Field bit settings" :
" Long Silence …….." followed by the comment that " You, ( ME The USER ) HAVE INTERFERED WITH The Settings of the previous French Heat Pump “Engineer".
I reset, the , now faulty, Heat Pump about 30 minutes after the Trio left with their tails between their legs.
Finally, A visiting Father & Son pair of “Engineers" :
Father , Shouting : “ I have never, in 30 Years experience with Heat Pumps ever installed a buffer Tank……."
Son , Quietly : " I am well aware that fitting a Buffer Tank is used to reduce the excessive “Short Cycling" that you clearly have experienced , my only comment would be the Size and position of the Buffer/Volumiser tank".
Why Do some, ( MOST !) “Heat Pump Engineers" , have such a low opinion of themselves , their industry, and their fellow competitor “Engineers"?
It’s a bad day for buffer tanks. @Brendon Uys is officially the Head of Domestic Heat Pump Design Net Zero at British Gas. He’s tasked with getting BG engineers to improve design and installation quality. It’s a big move on Brendon’s part, and hopefully, one that will lead to a speedier transition to higher ASHP installation quality on a mainstream basis.
I have been watching, with interest, the rebuild and replacement of a five year old Heat Pump on the Skillbuilder site.
The Results of the rebuild demonstrate How a heat pump should be installed!
The Skillbuilder channel has never given the cost of replacing the Heat Pump and the hot water tank, but the cost must have been substantial.
So , competent Heat Pump installers are available……………………………but unaffordable.
My own Heat pump has finally reached a COP of 4.5 ……………………but I DO NOT NEED A heat pump in these Temperatures.
As the NIC have repeatedly said of my Heat Pump …………………………NOTHING CAN BE DONE!
Abandon hope all ye who enter here!
A light-hearted, funny video that highlights the divide that exists in the world of heat pump installations as two titans clash over the industry’s most contentious issue – buffer tanks.
An interesting experiment on LLHs.
Interesting, but the question remains, why bother with a buffer in a typical domestic installation. Granted if you have another source of heating it might help with combining the two, but by far the majority of installations don’t.
It comes back surely to – if there isn’t a positive reason to fit it, then don’t – a comment which applies to almost any component of any system. Not only is it wasteful of resources and money but it may (and does in the case of heat pumps) introduce unexpected and undesirable effects. Furthermore if you don’t know why a component is there, how on earth can you spec it?
As expected, after publishing the buffer tank Homeowners’ Q&A episode below, we received a lot of pushback, comments, emails and DMs from pro-buffer installers. Needless to say we invited plenty of pro-buffer installers and they all declined.
The best-performing ASHP on heatpumpmonitor.org, installed by Damon Blakemore, doesn’t use a buffer tank, and many of the top 50 systems also skip them. Damon has always told me that buffers often aren’t sized correctly, and secondary pumps are rarely set up properly, which stems from poor design. The approach many installers take seems to be fixing problems rather than optimising performance.
Manufacturers include buffers to minimise volume and shift any flow issues to the secondary side, which avoids warranty problems. However, secondary pumps aren’t factored into SCOP figures when buffers are used, which skews performance data.
Stick to your guns (which I’m sure you will). Buffer tanks are, in most domestic cases, for the benefit of installers not homeowners. That being the case some installers will always argue for them, just as the fossil fuel industry will continue to argue that climate change isn’t a problem/doesn’t exits/isn’t caused by human beings/can be solved by hydrogen boilers…
Both are wrong for provable scientific reasons and their reason for claiming what they do is apparent for all to see (not that this is any excuse at all for spreading disinformation).
Keep up the good work!
Hello All. Thought I’d throw in my experience. When we had our ASHPs installed in 2011, it came with a largish buffer tank, for all the usual reasons such as instant hot water when the heating stats called for it.
After around 6 years in, after reading up on efficiency, I decided to remove the buffer tank. I reasoned that the system was wasting lot of energy simply keeping the buffer tank up to temp. A fact confirmed by our Plumber, who is experience with ASHP systems as it happens. Our system is quite large, so surely there was enough water buffering in the pipework with out the need for buffer tank, we opined.
So, we duly removed the buffer and made some tweaks to the pipework as necessary token the system flowing.
Results were staggering. Roughly 25% drop in energy input required to give same heat output. I have measured this over several years to eliminate a mild one off winter.
So no Buffer or LLH in our system seems to be the answer.
Hope this helps.
Cheers
Alan
Thats great to read!
Have you any detailed figures? Is the benefit more in shoulder season or in the coldest periods for example?
Thanks for sharing this and very pleased to hear the result. Well done for having the courage.
Its worth being aware that there are (at least) two reasons why removing a buffer tank saves energy, and its not necessarily heat loss from the tank that is the major contribution:
1. You aren’t having to replace the heat lost from the buffer tank – however if the buffer tank is inside the heated envelope the energy isn’t really ‘lost’, and anyway with a well insulated buffer tank it should be no more than 1-2kWh/day
2. A buffer tank, unless very well set up, results in a temperature drop between the flow from the heat pump and the flow to the emitters because flow and return mix in the tank. This means that the heat pump must operate at a higher flow temperature to get the same flow temperature at the radiators, and that means it is less efficient (lower COP) by very roughly 3% for each degree drop.
The latter is a function of the thermodynamics of heat pumps so doesn’t apply to fossil systems, which may be why some heating ‘engineers’ don’t understand it!
It is possible to set up a sufficiently tall buffer tank to avoid the flow and return mixing, and thus circumvent (2), but there are far too many reports where this has not been done (or is not even possible given the equipment/wiring used)
Hi all,
Trying to jump on an existing thread before creating a new one.
We’re looking at getting an ASHP installed and im having the buffer/no buffer deliberation.
Currently looking at a 5kW Vaillant and our system volume is ~200L.
Installers are speccing buffers and one even said because of the new R290s you MUST have a buffer – I can’t see this anywhere in research. Is this a thing, and if not any tips on how to push back?
(Bonus: this ‘experienced’ installer said that the unit doesn’t have to be >1m from the boundry is the fan isn’t pointing at it. It’d help… but I dont think they’re right)
@samiebon1, there’s a lot here that raises red flags with this installer’s advice, and I’d strongly recommend considering other options. This setup sounds like it could lead to complications down the road. Is this installer a one-man operation or a small company?
@Judith is spot-on about low-loss headers. After nearly two months of behind-the-scenes conversations with installers we’ve interviewed for the podcast, I can confidently say buffer tanks are rarely needed. In retrofit setups, volumisers can sometimes be appropriate, but that’s typically where it ends. So, no need to second-guess your decision. I don’t think this installer is right for you.
Where are you based?
@Mars @JamesPa Thanks both. The installer is part of a company (not one man band) and sounds experienced but the things they’re saying are a bit… odd.
They haven’t said volumiser, only buffer. I think i’ll push back a bit when they say Buffer (i’m an engineer so have some form of competence!). I’ve got a couple of companies coming to survey so will challenge and update you all!
Edit: Based in Manchester, England.
Check whether by ‘buffer’ they mean 2port volumiser (the key feature being 2 port). That’s ok. It’s typically 20-50l.. Vaillant do put a volumiser on most if not all of their system diagrams and sofaik it does no harm. It can go in flow or return (there are arguments both ways)but not between the two. Anything else – avoid.
Assuming you are in England then the 1m from boundary rule applies. I think it does elsewhere but would have to check to be certain.
…and any attempt to suggest otherwise is most certainly a red flag until proven to be a valid piece of advice. As @Mars said as well, what the potential installer has told you is rather screaming of “proceed with caution" at the very least.
@samiebon1 Sounds like some rowlocks are being bandied about to me…. Toodles.
You need to use Heat Geek, BG or Octopus to be certain of no buffer. You may get a volumiser (smaller tank in series) depending on your system. Don’t give in to LLH brigade!
One company who normally install buffers were willing to do a lower temperature system without one once the ‘estimating engineer’/salesman spoke to the boss. But we reasoned why go with a company with little experience of the design.
An update after I had some more interaction with those potential installers:
One had said the buffer was needed not technically but to cover manufacture warranty as thats how they specify the design (which made sense but would value other’s experience/input).
The other installer, when I challenegd on buffer and said the size of my heating system (~200L) he fully accepted that a buffer wasn’t needed.
Both however are still a bit lessay fair about the 1m distance and have only said it needs to have the fan pointing away. Makes technical sense and might be something along the lines of what I hear the MCS are looking to remove from requirements… but current guidance/requirments still says 1m.
@samiebon1, I can confirm that not installing a buffer won’t void the warranty. This comes directly from Vaillant, who do not require a buffer or volumiser but simply recommend meeting minimum system volume requirements.
This a matter of law not an MCS decision or even guidance. End of unless you want to apply for planning permission.
You mention it’s a Vaillant. As it happens I was looking at their their standard plumbing diagrams yesterday and certainly the one I looked at shows a 2 port volumiser (but not a buffer tank). What I’m not sure is whether the text clarified the conditions under which it’s necessary (basically if you haven’t got sufficient system volume). Unfortunately installers appear to have a habit of assuming that if it’s in the diagram it’s necessary, which is not always true.
Vaillant tech support are very helpful so you / your installer could ask the question.
Don’t accept a 3 or 4 port buffer, there are definitely diagrams in the Vaillant approved set that have only a volumiser so you are being given bs if they say a 3 or 4 port is necessary to cover manufacturers warranty. If they insist look elsewhere.