I’m a 51-year-old data networks (IP) architect with a strong interest in all things engineering and tech, and a confident DIY plumber. I had already refitted and added multiple radiators, baths and sinks to the house. After a huge amount of time spent six years ago (when I added the Evohome system to our boiler system) learning how the system worked and to troubleshoot various problems, I realised I was more knowledgeable than the typical “plumbing and heating” fitter about heating system architecture – and certainly more than the guys who put it in. Although I make no claims for the speed or neatness of my pipe fitting.
I’ve added extensive monitoring to my boiler system over the past five years, using Home Assistant, multiple ESP32/8266 boards (cheap microcontrollers) and DS18B20 temperature sensors (very cheap), culminating in me being able to analyse the heat needs of my house based on radiator and pipe temperatures all over it.
I added to this 30 minute logging of the gas meter (once I was able to get a smart one, took a while) using the Hildebrand Glow app. With those combined, I was able to set the flow temperature of my boiler much lower, aiming for a “low always on” behaviour rather than the “on@high , off, on@high” cycle typical of a boiler. This was not easy given boiler controls. That, and repeatedly measuring the “max kWh gas burned in an hour on a -5C day” (14-16kW), gave me the growing confidence to know my house would work with an ASHP – even though it is a 1970 build, 210sqm detached with insulation that could be improved.
Obviously I’ve done all the easy stuff – the remaining possible improvements are so disruptive and expensive I have not gone there yet.
Many people talk about fabric first but I decided my approach would be “the DIY-able and not hugely disruptive fabric first; then get off gas; then (maybe) the disruptive and expensive fabric stuff later”. Some will disagree with my approach, but that was my decision. In the former category I put in loft insulation and draught proofing. In the “maybe later” category I put improving the CWI (it’s a thin, poor-R-value system fitted at build time, which is hard to remove), maybe EWI, maybe dig/insulate the floors.
In 2020, I talked to a number of air source heat pump (ASHP) installer companies and even had one do a survey. All were keen for me to give them a large cheque (£20,000-£30,000) for a thinly or non-specified system on a promise of “we’ll totally rebuild all your heating and you’ll get it back through the RHI”. When I did my own in-depth research into component costs and added them up, I realised they were all trying to profit handsomely from the RHI, so I politely declined. Then the pandemic hit so works such as this went on hold.
During the same period (2019-2022), I put in PV, Tesla Powerwall batteries, got two EVs, and refitted (not myself) the kitchen to fully electric, all in a move to get off gas. This needed electrical upgrades to the house, but still remained single phase. I did investigate 3-phase with the DNO, but that was over £10,000 and we could make it work with single phase so decided to stay on 1P.
I found a very good company to do all of the above, but I couldn’t persuade them to do me an ASHP. The owner had DIY’d his own, which got me thinking – an ASHP , simplified, needs two pipes and a wire. There’s nothing that can explode if you get it wrong. Only the electrics require a qualified person. How hard could it be? Which got me thinking, do I DIY this?
I decided that 2022 had to be ASHP year. The Ukraine war and Russian gas were a factor, as was the climate change situation. I spent hours and hours on Heatgeek, John Seigenthaler and John Cantor’s YouTube channels and websites, understanding the details of the engineering and how to do the maths right. I did my own overall MCS calculations for heat loss (using Heatpunk) and built detailed room-by-room sheets for radiators, outputs and flow rates.
Once the Boiler Upgrade Scheme (BUS) grant came out, I tried again to talk to a few companies, but it became apparent that most were sticking £5,000 on their price once you did the maths on the components and T&M cost. Almost no one had any availability or interest in doing the work for me, which means in my experience you’ll be paying for it if you do get someone.
I was still very disappointed in the industry at that point. So I decided to start laying the groundwork for a DIY installation, still with an option to get a pro in later. As time went on I realised I may as well just DIY the whole thing – yes, I don’t get the 5k BUS cheque, but, I’ve not spent £5,000 on their cost uplift, so I am still neutral, and I will get the system I want if I design it myself, and can make sure all specs are exactly how I want them.
During the summer of 2022 I replaced six radiators and ran a new primary pipework to the ASHP location. The ASHP is actually directly outside where the boiler is, but I wanted new primaries as the boiler ones were way undersized for heat pump. The new primaries entailed floor lifting and joist drilling in my son’s room, so we bribed him with a new set of furniture once it was put back together.
The primary pipework bears some expanding on. Having spent time working out all those numbers, it becomes apparent that for 16kW at DT5, 28mm copper is OK-ish, but the numbers look a lot better with 35mm. But 35mm is expensive, the fittings are not available in the usual suspect stores, you have to go very specialist (whereas 28mm is ubiquitous) and is only press-fit requiring expensive tools or solder. Basically it’s for the pros. I did talk to a pro about him doing it, but it would have had to go a much longer way round through the main loft and been very expensive. So I opted for a hybrid approach, which comes out in my system schematic:
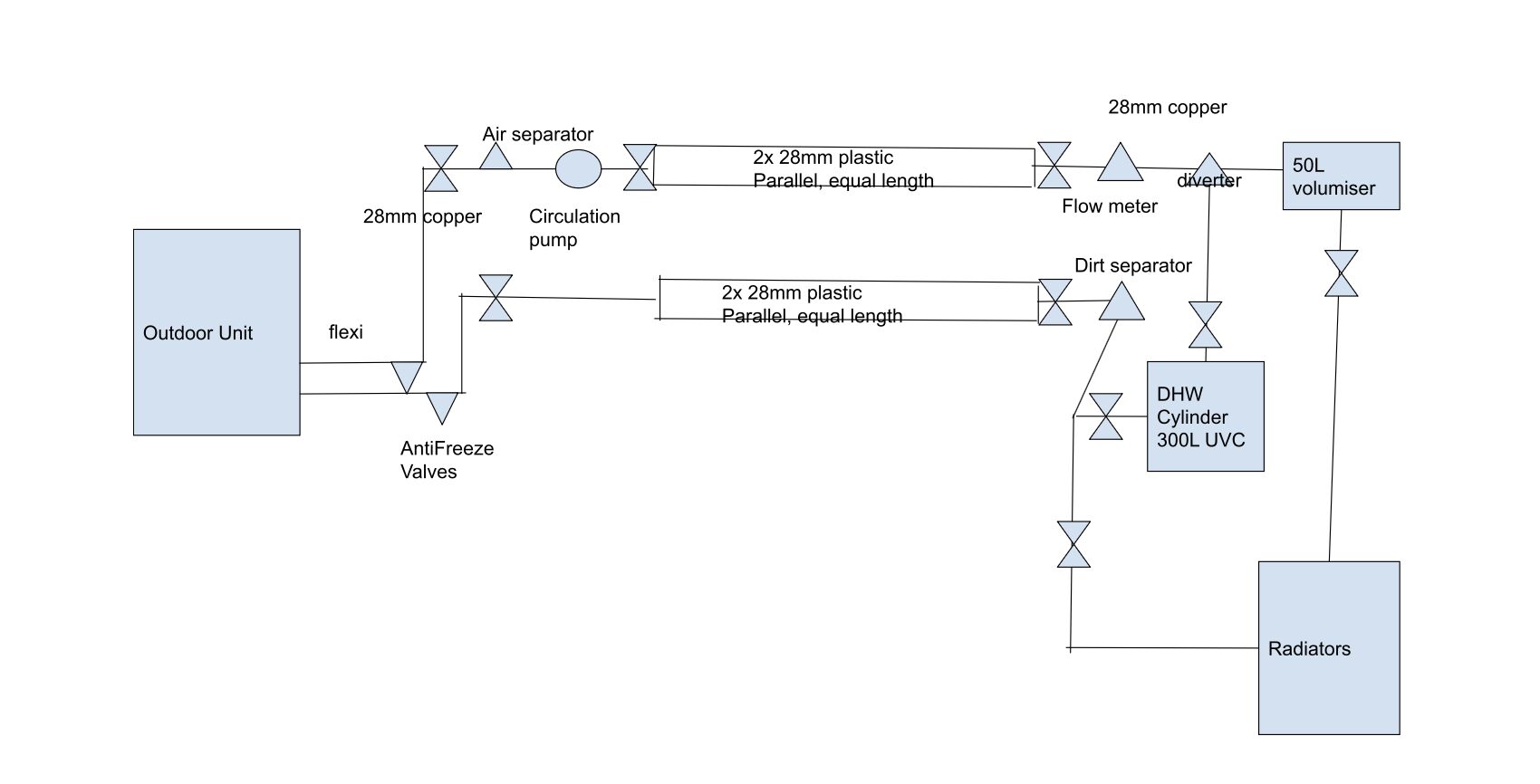
The pipework for the first few metres from the ASHP is 28mm copper (external part insulated using PrimaryPro). I’ve fitted antifreeze valves as I am not using glycol. This goes inside into a loft over the utility room (single story) where I’ve fitted the circulating pump and air separator. It then branches into two parallel 28mm plastic pipes for the long-haul (approx. 8m) to the airing cupboard.
This meant running 4x28mm plastic through the floor of my son’s room. Being plastic, I could do sweeping bends, no joints were needed and it was all a single run. It’s also considerably cheaper than copper and gave me a guaranteed leak-free route under my son’s floor (bearing in mind that the pipe was fitted six months before it had any water in).
It then goes back into 28mm copper for the section in the airing cupboard, where the volumiser, diverter and UVC sit, and the distribution to the radiators comes from.
There are isolation valve points everywhere, very useful when testing methodically, step-by-step.
A word on the air separator. We had horrendous air problems with our boiler-driven central heating system back when the boiler was moved to the utility – a long flat primary pipe run. These only went away when the boiler fitter added a Spirovent AAV to the flat section just upstream of the boiler. I knew that I was doing the same again, so had to have the same solution. I was also keen to have a proper magnetic dirt separator in the system rather than a basic strainer filter.
There is a lot of commentary out there that says you should not have components like magnetic dirt separators and AAV’s in ASHP systems because they slow the flow rate. In my opinion, this is something of an over-generalisation. But if you use standard 28mm units from a plumbers’ merchant intended for boiler use, they will indeed do that, as they have a high internal pressure loss at the flow rates needed for an ASHP. I suspect this is where the simplistic view comes from.
If you take the time to research pressure loss curves of components and go up a size, then there are several that have acceptably low losses at ASHP flow rates. I selected the Spirovent AAV in 1 ¼” BSP sizing, and the Spirotrap MB3 dirt separator again in 1 ¼” BSP. Note that while these are both available (and cheaper) in 28mm, I felt that the lower pressure loss of the larger size was necessary. 1 ¼” BSP to 28mm adapters were then needed. I thread glued them in with Loctite 577.
The diverter setup is also a component to be chosen carefully. A typical 28mm 2-way or 3-way central heating zone valve has again very high pressure loss at ASHP flow rates. I was amazed when I took the ones off my system (that were for the boiler) and saw just how thin the inner bore is. After feedback on the Renewable Heating Hub forums from Brendon Uys (Heacol) to look at Bellimo or ESBE, and again a lot of time on manufacturer websites, I selected the ESBE VRG131 valve – again in 1 ¼” for lower loss. This also needs an ESBE ARA actuator (aka zone valve head) as they are separate components. These together do cost a lot more than a typical central heating zone valve.
It’s worth saying that these key components – AAV, Mag separator, Diverter – were key factors in the overall pressure loss calculations. They were also significantly more expensive and harder to find than the typical 28mm alternatives.
I decided on my final design in January 2023 after reading a lot more from Brendon Uys, Marko Cosic and Graham Hendra, to go with a single loop (no buffer) to avoid buffer distortion loss, but recognising that that made me responsible for getting the flow rate and volume design and engineering right.
I went for a Samsung G6 as my ASHP as they are mass market units, tried and tested, well-priced, available from several places, good MFR documentation, there are good third party training videos for installers (thanks Graham Hendra) and the manufacturer’s training is free (I went on it).
The separate pump means if you need a bigger pump, you can fit one – in my view that’s a good thing. The final decider was the availability of a modbus interface to allow me to monitor it directly (from Home Assistant, along with all my other stuff). The hope being that eventually I can also optimise its performance by sending control signals such as increase/decrease output or temperature using modbus rather than relying on MFR controls which will inevitably be limited in one way or another. The downside is that although natively it does weather compensation it doesn’t do load compensation much (if at all). There are third party companies (Homely) doing this as an add-on, via modbus, so I knew it would be possible.
Physically fitting the volumiser, diverters, etc. was interesting as there isn’t a lot of space in the airing cupboard – I spent hours searching MFR specs for different shapes and sizes buffer tanks that I could use as a volumiser. None of the pros I spoke to previously were prepared to fit in there. They all said “all the stuff will have to go in the loft” which would have been simpler and quicker for them, but I really wanted to stay inside the heated envelope for long-term efficiency. So I spent a lot of time trying different pipework arrangements until I found one that I could make fit. A benefit of being a DIY’er – a pro would have just said, “It won’t work I need to put it somewhere else.”
My 17-year-old son helped me lift the ASHP into its final location – a heavy two-man lift but some inexpensive “shoulder dolly” lifting straps from Amazon did the trick.
During all this time the house was still running on the boiler – I hadn’t touched the primary side of that. Obviously, I had done a lot of work on the secondary side during the summer with the new radiators, but I just put the boiler system back working as autumn started.
Building the ASHP with new primaries allowed me to wet test all the way from the ASHP to the volumiser during February, without affecting anything in the house that was keeping people warm, and temporary bypass loops allowed me to commission the ASHP fully.
I finally got enough of a window to cut the system over on March 25, 2023. My target was by end of March, so I’m really pleased to have hit it.
Partial drain down, move the radiator connections in the airing cupboard to link into the ASHP primary side, refill and test. No heating for only about two hours. I switched the boiler off on its electrical isolator and off at the gas meter – that was very satisfying.
I’m thrilled to say it’s all working nicely and we’re running on the ASHP. After one day, with outside temps at 6C, the house is staying at 20C with an LWT of 38, so I’m very happy with that too.
There’s much tuning still to do – I haven’t rebalanced yet, and there is some radiator zone distribution pipework that could be “fatter”, and I want to add some FCUs for extra output in a couple of rooms (and probably for cooling as well). That will have to wait till summer. I announced over dinner to the family last night that “We’re on the ASHP now” and no had even noticed. Success.
Hi Ian, interesting article. Im doing the same thing myself and am almost ready to connect my 5kw Samsung Gen 6 to the central heating pipes. I have previously installed a Mitsubishi Ecodan 11 years ago connected to UFH. I have been running my gas combi at 40 degrees C over the winter months and upgrading the rads as needed so im confident I will have enough heat.
Im also using a mix of copper and plastic pipes (my previous install just used 22mm plastic which worked fine it seems) but Ive gone with 28mm copper to the HP and then using the existing 22mm copper CH pipes down to 15mm plastic to the rads.
With respect to constriction of flow rates by valves etc, one of the arguments against using plastic is the constriction caused by the smaller bore and pipe inserts and fittings. Ive used metal inserts to try and minimise this but ive also read on John Cantors website that short restrictions dont actually make much difference to the overall flow rate so it may well not be an issue.
Mark
Hi, I am going to install Samsung HT Quiet ASHP and plan to have underfloor heating/cooling. For cooling, we need to take into account the dew point, which is a function of the temperature of humidity. Do you have any experience/git hub source code to do that?
As I understand it, it is not possible to do a full DIY install of ASHP for two reasons. Firstly, any electrical work must be completed by a qualified person, this is obvious. Secondly, although pre plumbed hot water cylinders are available, and in my view make this much simplified, there is another “G3” qualification required to install a unvented cylinder because it is a pressurised vessel. Without the correct paperwork building control will not sign it off. Without this, you will have issues if you ever come to sell the house.
I’m therefore surprised that the article does not mention the install of the hot water cylinder….
Neither of those are actually the heat pump itself, so were not the focus of my post. Both were done by qualified persons. the DHW cylinder by a G3 certified heating engineer 1 year before, and the electrical side by a qualified electrician. I certainly wouldn’t do either of those myself either.
Fortune favours the brave. Great article. Thanks for sharing
Hi Ian, I think you’re right about the BUS grant just bumping up the quotes. So I went for two a/c units that are enough to heat the house. I’d still like to have warm water in the rads occasionally though and stop using the immersion for DHW. Did you look at a monoblock ASHP and hydronic system? I’m struggling to see why we can’t just take the pipes off the gas boiler and put a heat exchanger in its place? I already have a building control system that could manage the whole thing. Any thoughts?