It’s always rewarding to complete a project and receive great feedback from a happy homeowner. This was the case with a recent installation of an air source heat pump in a solid stone property; one that many in the industry might have deemed unsuitable for a heat pump without a completely new heating system.
Here’s what the homeowner had to say:
“Our new ASHP system was installed in mid-January, and for the first time in 16 years, the house has been consistently warm – especially my home office, where even in mid-summer, I previously needed a pullover. We haven’t had to use the log burner in several weeks.
We upsized two radiators, relocated one, added a new one for thermosyphon and discovered that our underfloor heating valves were not fully functioning. Downstairs is a consistent 20–21°C, and upstairs 17.5–18°C when it’s 0°C outside.
The plant room has been returned to a utility room, which means everyone is happy.
Brendon and Jordan from Heacol have been with us throughout and have consistently stepped up to improve the system and resolve any niggles.
This included replacing the awkward inline filter with one in the plant room, adding open-source accurate monitoring and installing an interior thermometer so that the unit reacts to the house’s inside temperature rather than just the flow temperature. A communications issue with the outdoor unit required a temporary workaround, but this was resolved quickly.
The system is now accurately responding to both outside temperature and energy demand. Yes, this is a big house with a big heat loss (220m² @ 99W/m²), but we now have a system that works, and we expect running costs to go down compared to the two previous 16kW systems.
Thanks, Heacol, for working continuously to design, install, and refine the system.”
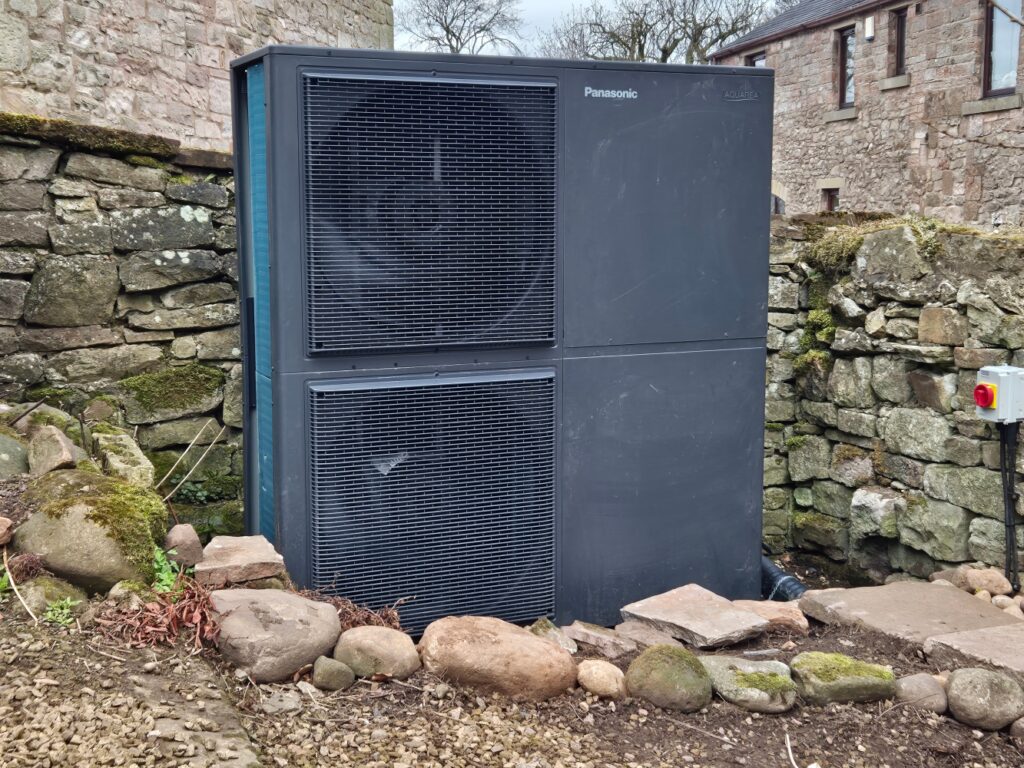
This project came as a referral from a user on the Renewable Heating Hub forums, further demonstrating the value of shared homeowner experiences and expert guidance and the importance of finding the right installers.
Challenging Industry Assumptions
Many in the heating industry claim that installing a heat pump in a solid stone, uninsulated, single-glazed, draughty building with poorly designed underfloor heating (250–300mm centres) is impossible without a completely new heating system. The existing setup in this home included 25mm Pex-Al-Pex primary pipework feeding both underfloor heating and radiators, with some terminating in 12mm Pex-Al-Pex.
However, rather than dismissing the project as unworkable, we designed the system based on first principles and careful calculations.
System Design and Performance
- Heat Load & Flow Rate: The property’s heat load was calculated at 21kW. At a ΔT of 8°C, the required flow rate was 43L/min. The Panasonic M Series 25kW heat pump’s internal pump was able to achieve this.
- Underfloor Heating: The system had only four circuits covering nearly 100m² of floor space. With a total flow rate of 22L/min (just over 5L/min per circuit), velocity was a comfortable 0.77m/sec. Friction loss was calculated at 8.86m head (86.86 kPa), which was manageable for the heat pump’s pump.
- Radiator Distribution: The 25mm Pex-Al-Pex pipework supplied two manifolds. The first, located 7m from the plant room, served six of the nine radiators, requiring a peak flow of 21L/min with a pressure loss of 1.96m head (19.6 kPa). The second leg, serving three radiators, had a flow of 7L/min, with minimal pressure loss (0.26m head, 2.6 kPa).
- Radiator Sizing: Two radiators were replaced. The largest and furthest was an Ultraheat 600×1600 6-column radiator delivering 2.3kW. Despite being supplied by 18m of 12mm Pex-Al-Pex, at a ΔT of 8°C, it required only 4.1L/min, with a friction loss of 5.19m head (51.9 kPa) and a velocity of 1.18m/sec (well within acceptable limits).



The Results
The homeowner’s feedback confirms that the system is performing exceptionally well, maintaining stable indoor temperatures and reducing running costs compared to the previous two 16kW heat pumps.
This project showcases that with the right design, a heat pump can successfully operate in what might be considered a ‘worst-case scenario’ for microbore systems. The key is to approach the installation based on hydronic principles, not outdated industry assumptions.
The Buffer Tank Myth
One of the most persistent misconceptions in the heating industry is that buffer tanks are necessary for microbore systems because they cannot achieve sufficient flow rates. This claim demonstrates a fundamental misunderstanding of thermodynamics and hydronics.
- Heat transfer is about water movement: If water cannot move efficiently, neither can heat. If a system struggles to maintain the desired ΔT of 5°C, the house will be cold.
- A buffer tank does not improve flow rates: Instead, it creates the illusion of improved performance by allowing higher flow to the heat pump while restricting flow to the system, ultimately increasing running costs.
- In modern modulating systems, a buffer tank is rarely necessary: Properly designed systems, using the right equipment and controls, will perform well without one.
Closing Thoughts
This case study highlights the importance of applying sound engineering principles rather than blindly following industry norms. Despite widespread misconceptions, microbore systems can function effectively with the right approach. In over 400 similar installations, we have never had to completely re-pipe a system – alterations, yes, but never full replacements.
Heat pump installations should be based on careful calculations, not assumptions. This project proves that even in challenging properties, a well-designed system can provide excellent heating performance and efficiency.
A sensible install. Well done.